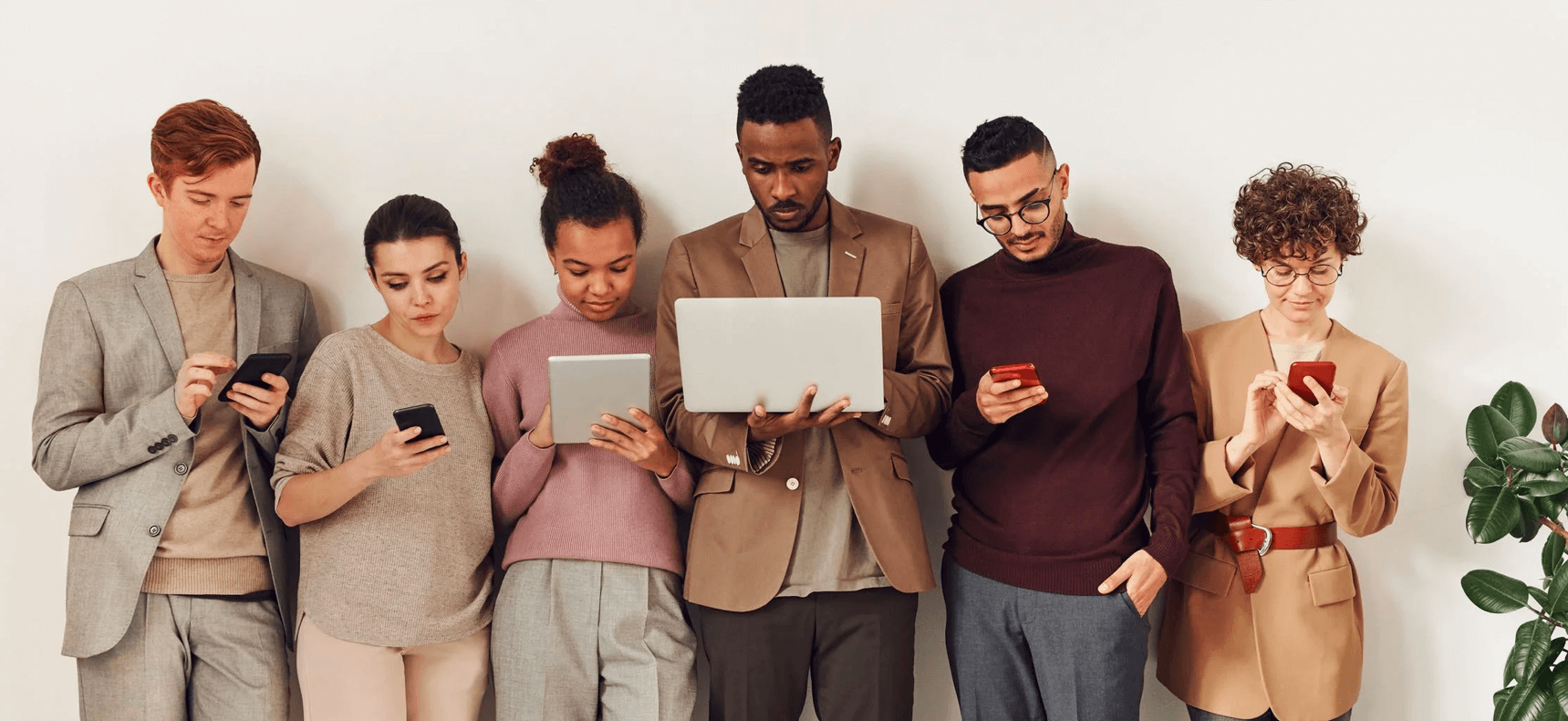
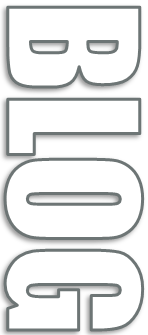
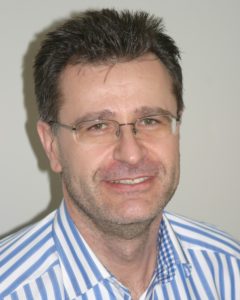
Written by Rick
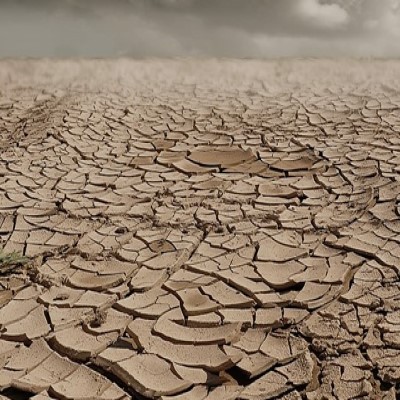
Dry Running of the Diaphragm Pump
Dry running is a one of the key features that differentiate Air Operated Diaphragm pumps from other types of pumps. In majority of the cases this will not damage the pump, nor its elements. This is why, AODD pumps are often used in applications in which the fluid may unexpectedly run out (sumps dewatering, tanks and cisterns transfers, etc.).
However, we should be aware of the few side effects resulting from dry running of the pump and costs and risks associated with it.
When running dry the Diaphragm Pump will not overheat – there are no surfaces which will rub with one another causing excess heat generation. Also, AODD pump suction cavitation is not as destructive as in case of rotary pumps. However, it is not recommended to run dry constantly or for long periods.
Dry running is unproductive and expensive. Diaphragm pump which run dry speed up. A dry running pump can operate two to three times faster than it does when under load. This will result in bigger air consumption (electricity cost), and unproductive consumption of diaphragms cycles. Due to increased pump speed during run dry operation diaphragms will make a lot of “empty” strokes decreasing own elasticity (ability to return to its original shape after it has been stretched) what result in shorten lifetime.
In a case of PTFE diaphragms rapid decrease of elasticity may lead to serious consequences. PTFE diaphragms are not as resistant to dry running as diaphragms made of other materials. A downfall of PTFE diaphragm is resilience. PTFE has no “memory”, is not capable to revert to its original shape after deformation.
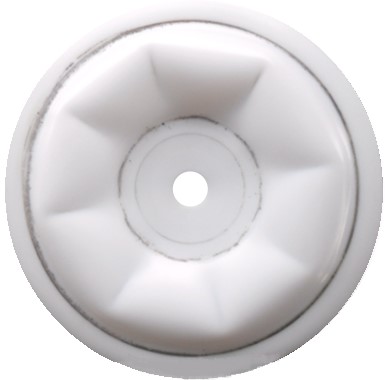
We should be aware of fact, that there are many grades of PTFE from which diaphragms can be made. This PTFE diversity in grades and qualities results in considerable differences in diaphragms performances and longevity. After PTFE diaphragm is flexed, voids or air pockets are created in the material making potential for fluid to permeate into the PTFE. It happens, that fluid permeation occurs without noticeable damage to the diaphragm. However, this weaken PTFE and may reach the point in which fluid will pass through the diaphragm and chemically attack not wetted part of the pump.
Knowledge of such a risk resulting from dry running of PTFE diaphragms is essential when handling hazardous fluids and fluids with a small molecular structure. Hazardous liquid inside non wetted part could damage the pump, ruin manufacturing process, contaminate environment and put people life at risk.
Users of larger size pumps (1 1/2” – 3”) with PTFE diaphragms should be especially alerted to the dry running. Lifetime (number of cycles) of these diaphragms is significantly lower, than smaller sizes PTFE diaphragms. Additional reduction of their lifetime caused by dry running can have dramatic consequences.
Double layer PTFE diaphragms with a backing rubber material (like Neoprene, EPDM, Viton) possess improved flexibility, however PTFE layer is still prone to deformations. Fluid permeation can still occur causing adhesive (used to bond two layers together) decomposition, diaphragm delamination and chemical attack on the non-wetted part of the pump.
Usage of two separated diaphragm – PTFE on the liquid side, other material on the dry side of the pump improves PTFE flexibility, but not to the extent to eliminate the problem.
Summarizing – prolong dry running of the AODD pump is expensive and risky. This means more air usage and faster wear and tear on the pump. Pump maintenance costs goes higher. The risk of unexpected pump failure goes up.
There are several solutions to this problem.
Inexpensive – liquid level visual monitoring by personnel. Observation of dry running symptoms during pump maintenance, service works.
More expensive – fluid level control- usage of variety of liquid level sensors – floating, radar, ultrasonic, optical, capacitance, conductivity or resistance, etc. Or, YTS pneumatic fluid level controller with diaphragm pump control system.
More expensive – air monitoring controllers – air monitoring controllers turning the pump off when the air usage indicates that the pump is running dry. Dry-running pump faces almost no resistance. Therefore, it operates two to three times faster than it does when under load while consuming significantly more air.
There are mechanical controllers, which operates without power. They are difficult to set up and can be unreliable when pump working conditions change (for example, pump discharge pressure).
More reliable are electronic air monitoring controllers based on logic programing which better detects when diaphragm pump is truly running dry, attuning itself to the changes in pump working conditions.
We’ve got something exciting to tell you!
HELLO SWEDISH! We’re excited to announce that we’ve just launched Swedish language support on our website! This new addition to our language family has been
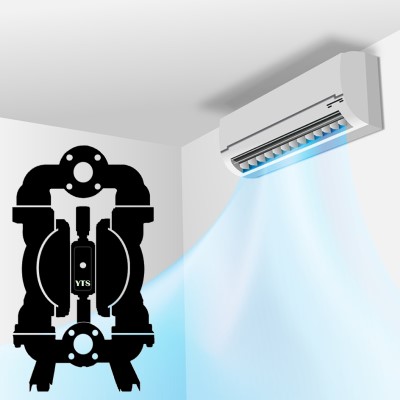
Indoor Air Quality
Indoor Air Quality (IAQ) – air quality within and around buildings and structures plays is of utmost importance not only for employees well-being and ability
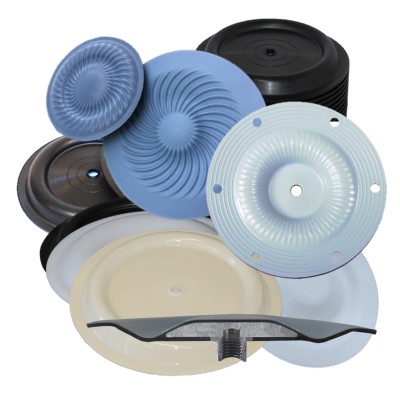
10 Factors to Consider When Selecting Diaphragm
Diaphragms are one of the most important elements of Air Operated Double Diaphragm Pump. They separate the wetted side (fluid side) of the pump from
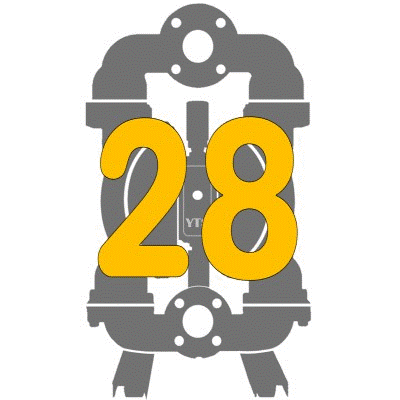
28 Reasons Why Use Air Diaphragm Pump
Air Diaphragm Pumps are so much versatile in design, materials, performances and functions, that they can handle most types of fluids. They are used for
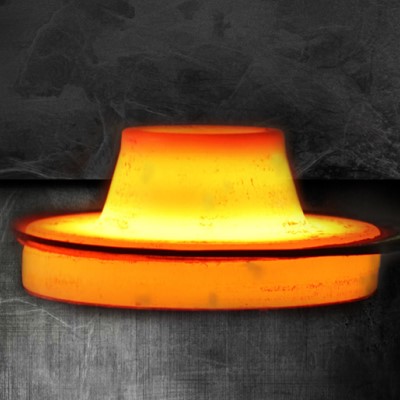
Hastelloy Air Diaphragm Pumps
The primary function of Hastelloy C-22 (also known as a “superalloy” or “high-performance alloy”) is a long-lasting survival in severely corrosive, or erosion prone environments,
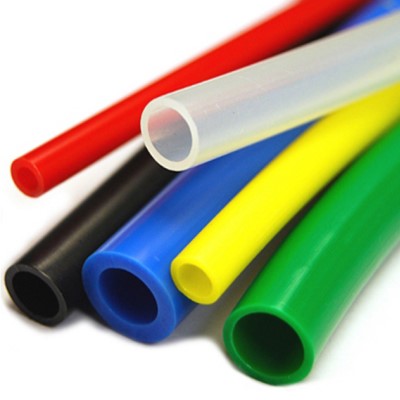
Too Small Size of Air Supply Line to the Air Diaphragm Pump
It is not uncommon to use too small air supply line when installing an Air Operated Diaphragm pump. Overlooking restrictions installed along the line, which
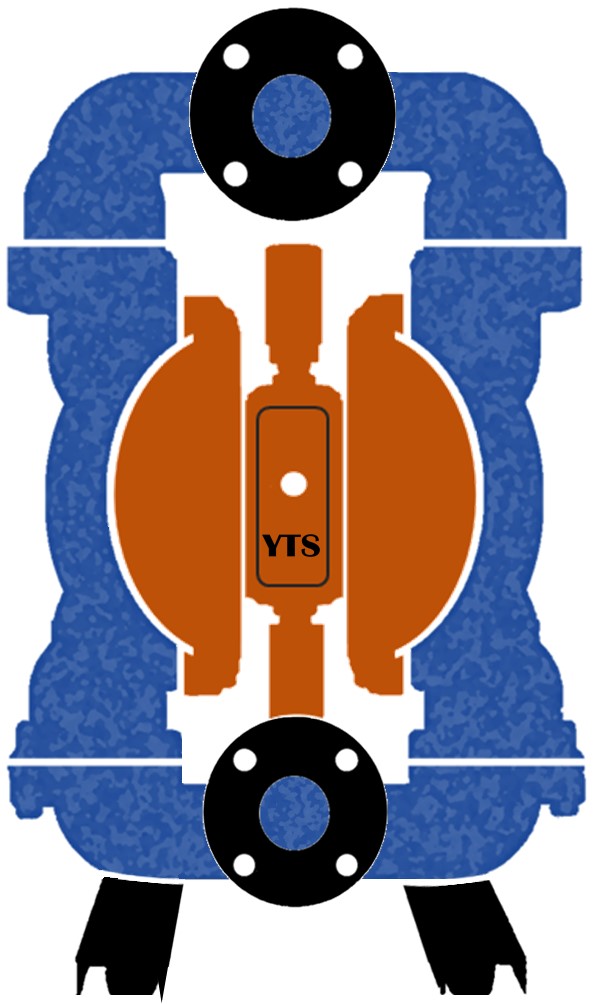