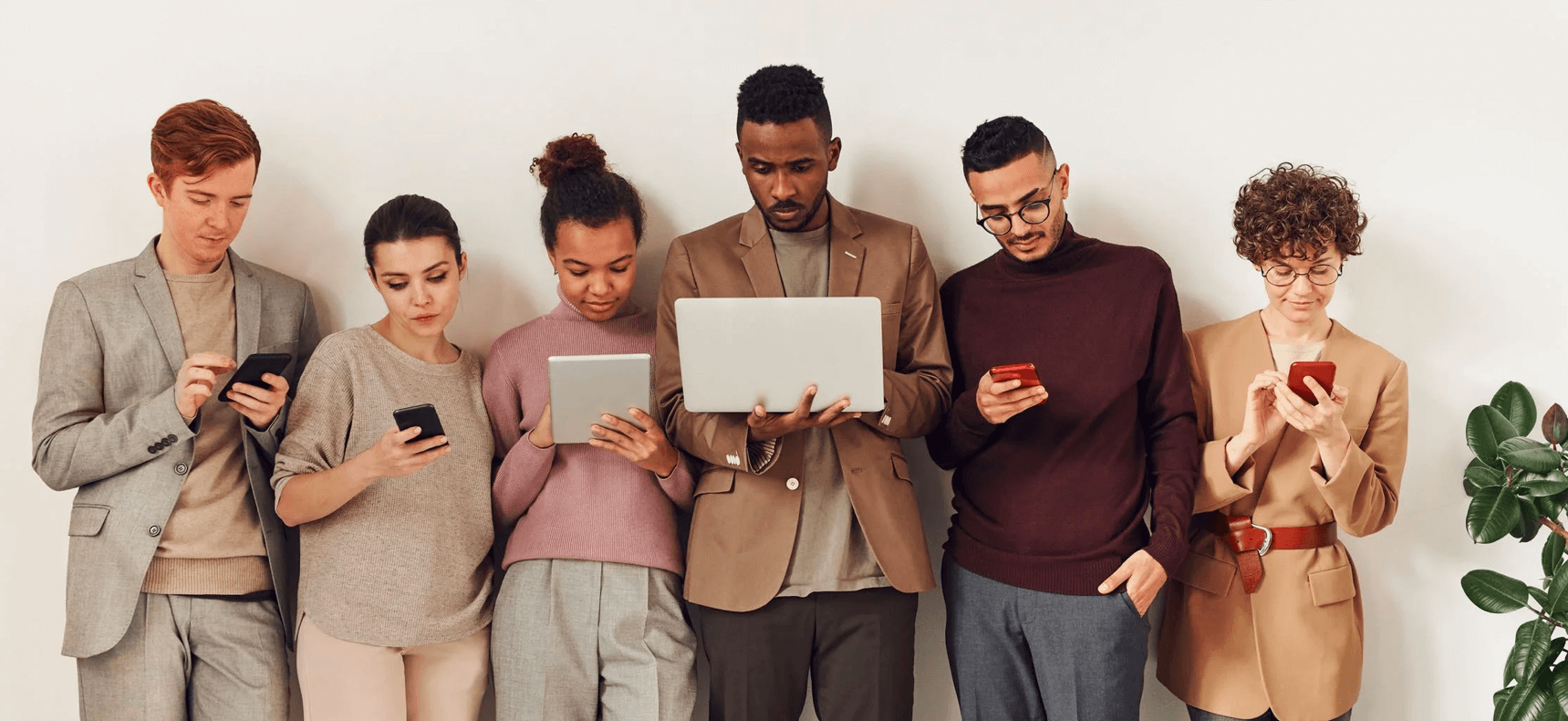
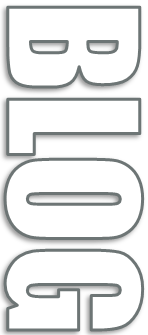
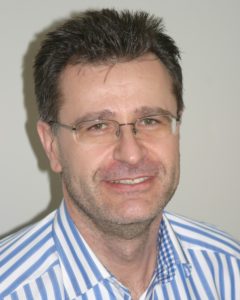
Written by Rick
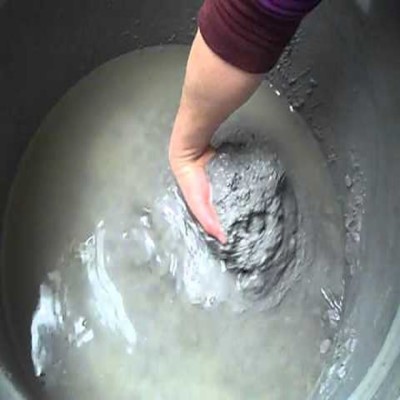
Abrasive Applications
In the second article from the cycle 12 ways how to kill your Diaphragm Pump I will concentrate on the ways how to handle Abrasive fluids. Abrasive fluids can be very destructive to the pump if not handle properly. They cause increased damage to the pump elements by gradually wearing away surfaces through physical force.
Physical erosion arises from the action at the pump elements of solids carried within the pumped fluids. In many cases, physical erosion significantly speeds up chemical processes of corrosion, what can lead to pump destruction in a short period of time. Solids abrade outer shells of pump components, exposing inner material layers for further corrosion.
Abrasive liquids are those which carry minerals or inorganic substances, that are harder than the material they rub against. There is a wide array of different type of abrasive liquids, such as lime-scale, clay, paint and ink pigments, carbon or metal fines, etc. Some of them, like for example printing inks have minimally abrasive characteristics, with pigments that tend to be softer and finer, while some paints have harder, coarser pigments and extremely abrasive properties.
The first consideration when selecting AODD pump to abrasive application is to find out abrasiveness of the liquid, which is determined by the characteristics of the solids (material hardness, size, shape), their concentration and viscosity. The second consideration is pump material (pump body, diaphragms, valves), and pump working conditions – in particular the pump speed – air pressure.
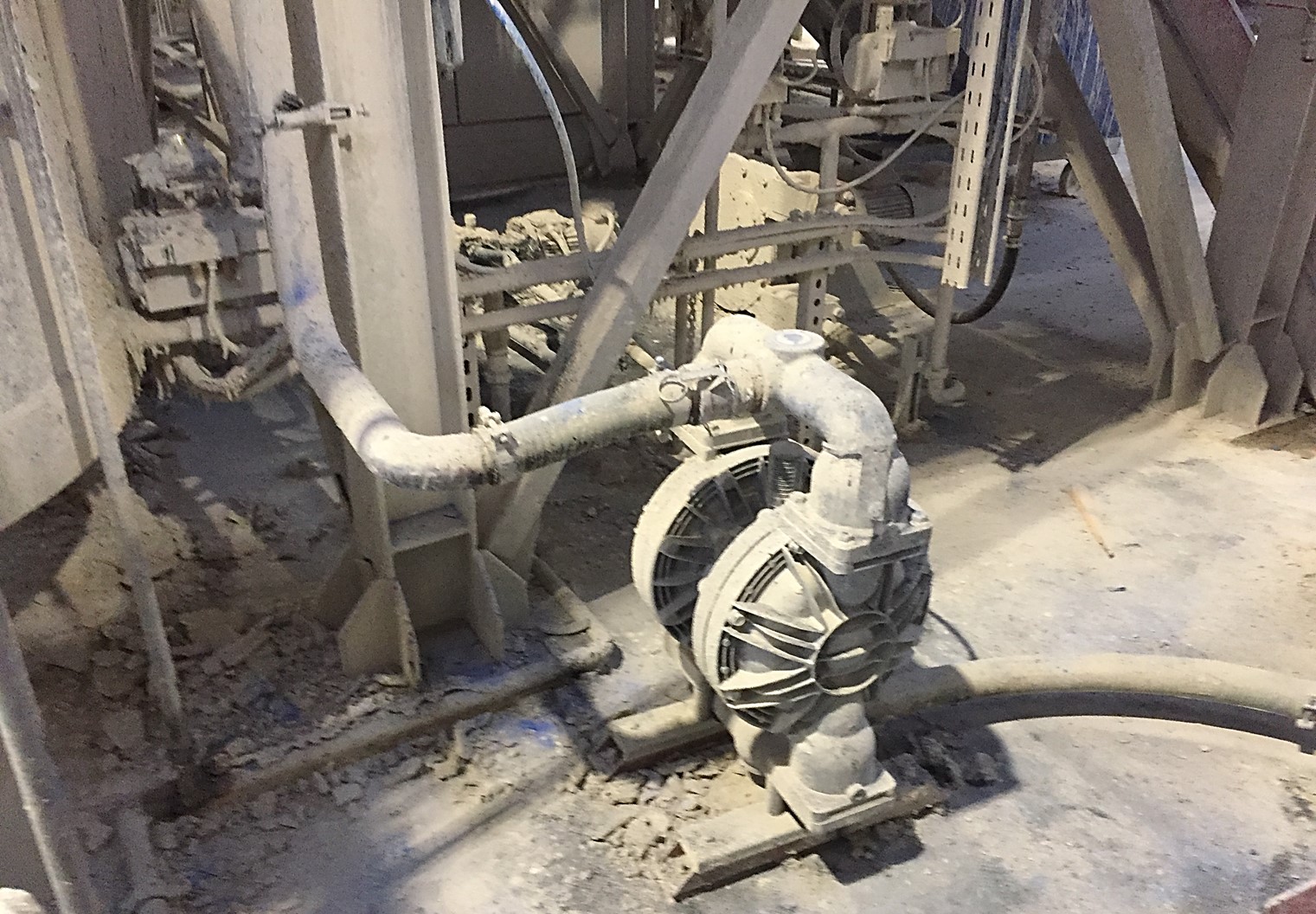
The hardness or scratch resistance is measured using six main hardness tests: Vickers, Rockwell, Brinell, Mohs, Shore and Knoop. The Rockwell and Mohs are probably the most commonly used hardness tests in pump industry. Mohs scale ranges from 1 (talc) to 10 (diamond). Aluminium has a rating of 2,5 – 3,0; Cast Iron 4,0 – 4,5; and Stainless Steel 316L 5,5 – 6,3. Abrasion becomes a serious problem when solids hardness exceeds pump material hardness.
In addition to hardness, the shape and size of solids are important factors in determining wear. Solids with sharp edges will very quickly damage diaphragms and balls. In general, higher concentration of solids, the greater wear to the pump. Nonetheless, the particles size and hardness affect the level of abrasion more than large concentration of small particles.
To determine proper liquid abrasiveness its viscosity should be known. High viscous fluids create protective film on pumps components. Such a protective film cushions the impacts of solid particles, reducing wear (sand in oil is much less abrasive than sand in water).
Pump design plays important role when dealing with abrasive liquids. Pumps with lower area and time during which solids rubs elements of the pumps are more resistant to action of abrasive fluids. Short Stroke Design of YTS Diaphragm Pumps makes them perfect pump to use in abrasive applications.
Generally, to combat abrasion and reduce spending on spare parts and new pumps is recommended to use larger pumps running at lower speeds. Lower pump speed (less air pressure at air supply line) reduce liquid velocity. The lower pump speed, the lower speed movement of solids in the liquid – less impacts with pump components. By halving the speed of AODD pump, the wear may be reduced by a factor of four or more. Depending on liquid abrasiveness Diaphragm Pumps that works on speeds one third to one half of rated speed are commonly used in many abrasive applications.
The initial investment in larger pump is more costly, however this will quickly pay off. When working with abrasive fluids costs less to use a larger, slower pump that will last longer, rather than frequently replacing or rebuilding a smaller, faster pump.
However, what to do in cases in which the use of larger pump is not possible (economic reason, the larger pump is already used, space limitation)?
There are still ways to protect pump against wear. One of them is to use YTS Anti Abrasive Pads.
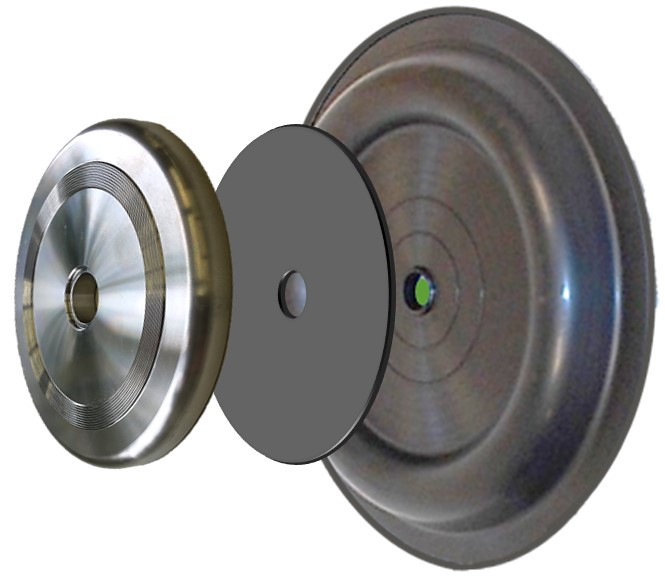
We’ve got something exciting to tell you!
HELLO SWEDISH! We’re excited to announce that we’ve just launched Swedish language support on our website! This new addition to our language family has been
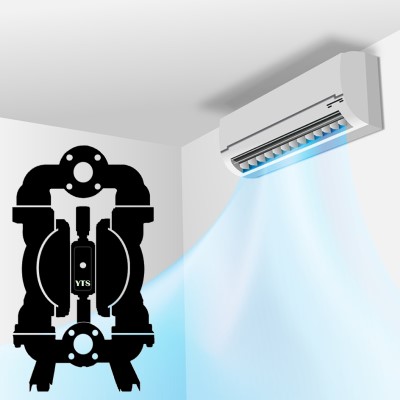
Indoor Air Quality
Indoor Air Quality (IAQ) – air quality within and around buildings and structures plays is of utmost importance not only for employees well-being and ability
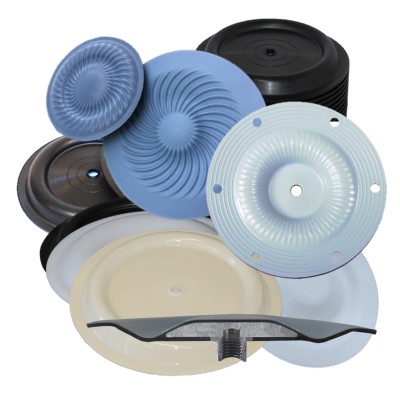
10 Factors to Consider When Selecting Diaphragm
Diaphragms are one of the most important elements of Air Operated Double Diaphragm Pump. They separate the wetted side (fluid side) of the pump from
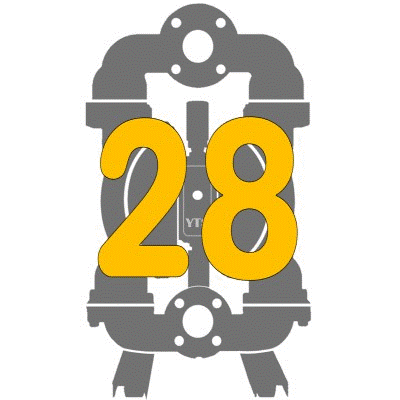
28 Reasons Why Use Air Diaphragm Pump
Air Diaphragm Pumps are so much versatile in design, materials, performances and functions, that they can handle most types of fluids. They are used for
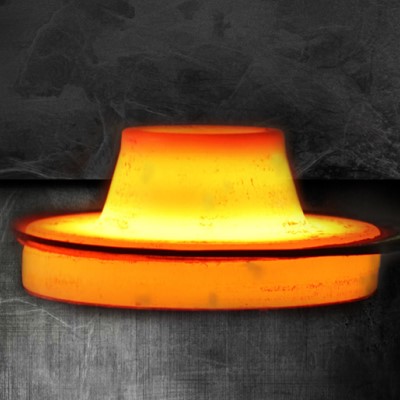
Hastelloy Air Diaphragm Pumps
The primary function of Hastelloy C-22 (also known as a “superalloy” or “high-performance alloy”) is a long-lasting survival in severely corrosive, or erosion prone environments,
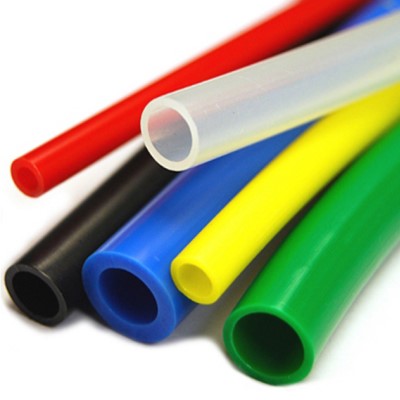
Too Small Size of Air Supply Line to the Air Diaphragm Pump
It is not uncommon to use too small air supply line when installing an Air Operated Diaphragm pump. Overlooking restrictions installed along the line, which