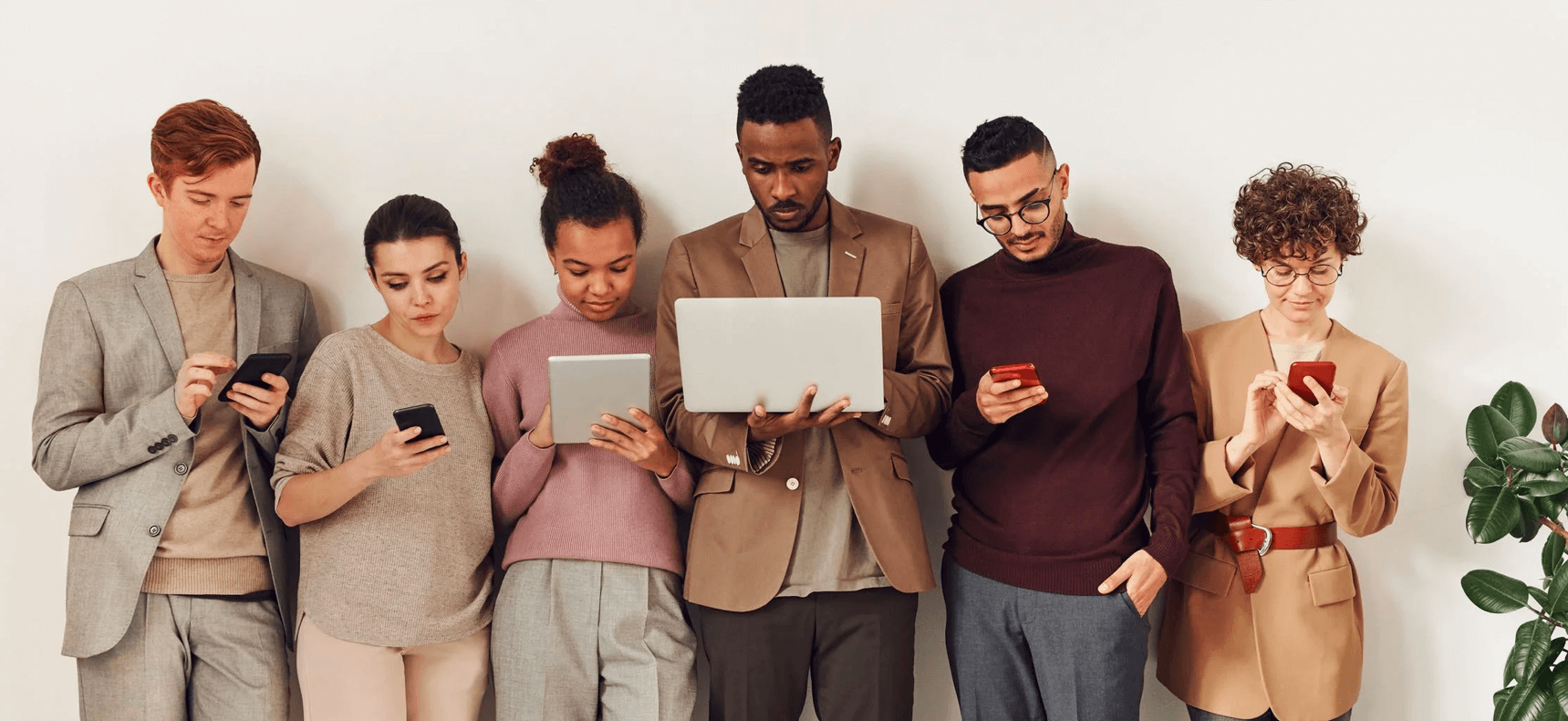
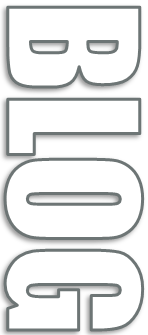
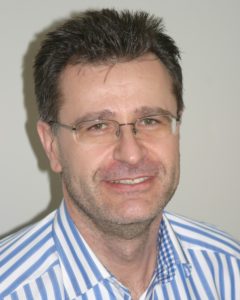
Written by Rick
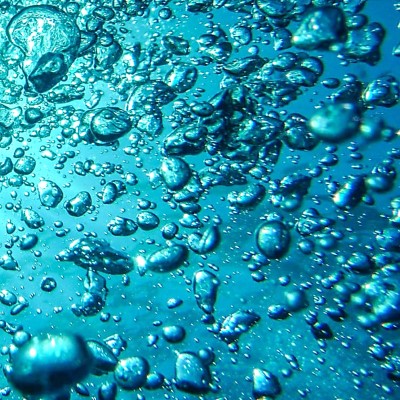
Pump Cavitation (suction cavitation)
Cavitation is a common problem in pumps, including Air Operated Diaphragm pumps. Cavitation can cause significant damage to the AODD pump, which in turn can lead to the spilling of pumped fluid and potential risk to installation, facility and personnel.
What is cavitation?
Cavitation is an occurrence in which rapid changes of pressure in a liquid lead to the formation of small vapor bubbles. Rapid collapsing of these vapor bubbles produces shock waves inside the pump.
If the liquid pressure on the suction side of the pump drops to the vapor saturation pressure the vapor bubbles begin to form in the liquid. The lower the pressure, the more bubbles begin to form in the liquid. We can describe this process as a “boiling” of the fluid.
We know, that fluid temperature of boiling depends on pressure. A liquid at high pressure has a higher boiling point. The boiling temperature of a water at the sea level is higher, than in the mountains. For example, the atmospheric pressure on the top of Mount Everest is slightly over 0,3 bar, and water there begin to boil at a temperature of around 70°C.
On the suction side of the pump, the pressure can be significantly lower than atmospheric. As a result, the liquid begins to “boil” with the formation of vapor bubbles. When the liquid moves to the pump discharge area (where the pressure is higher than atmospheric pressure) the vapor bubbles quickly collapse, creating a shock waves of incredible force and causing vibration in the liquid. These shock waves can be very strong, striking pump elements even at a rate of 10.000 times per second.
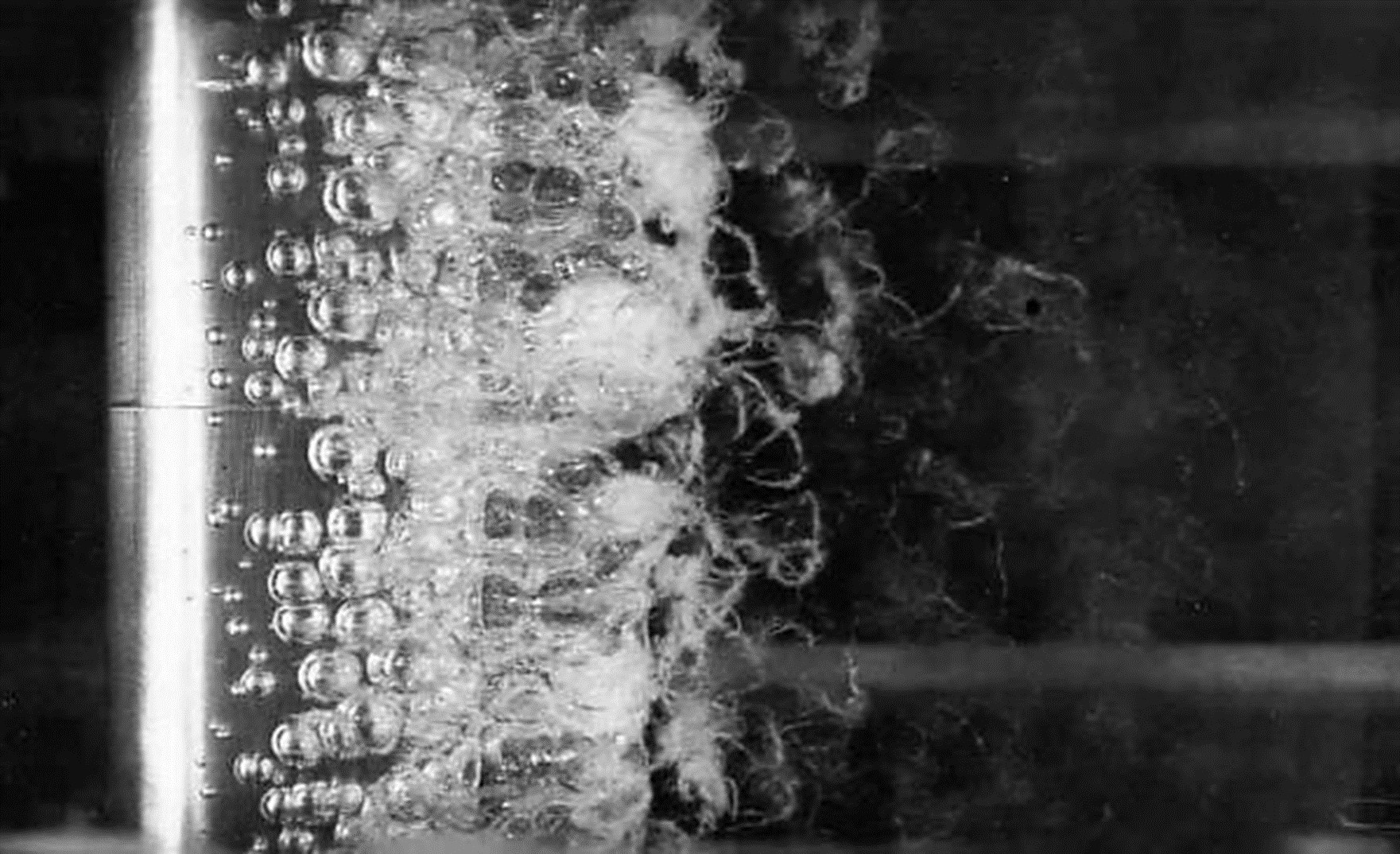
Naturally, these violent waves lead to the destruction of diaphragm pump elements – valves, diaphragms even pump body fractures. In addition, cavitation bubbles cause a point increase in the temperature of the liquid, which combined with vibrations accelerates pump damage process.
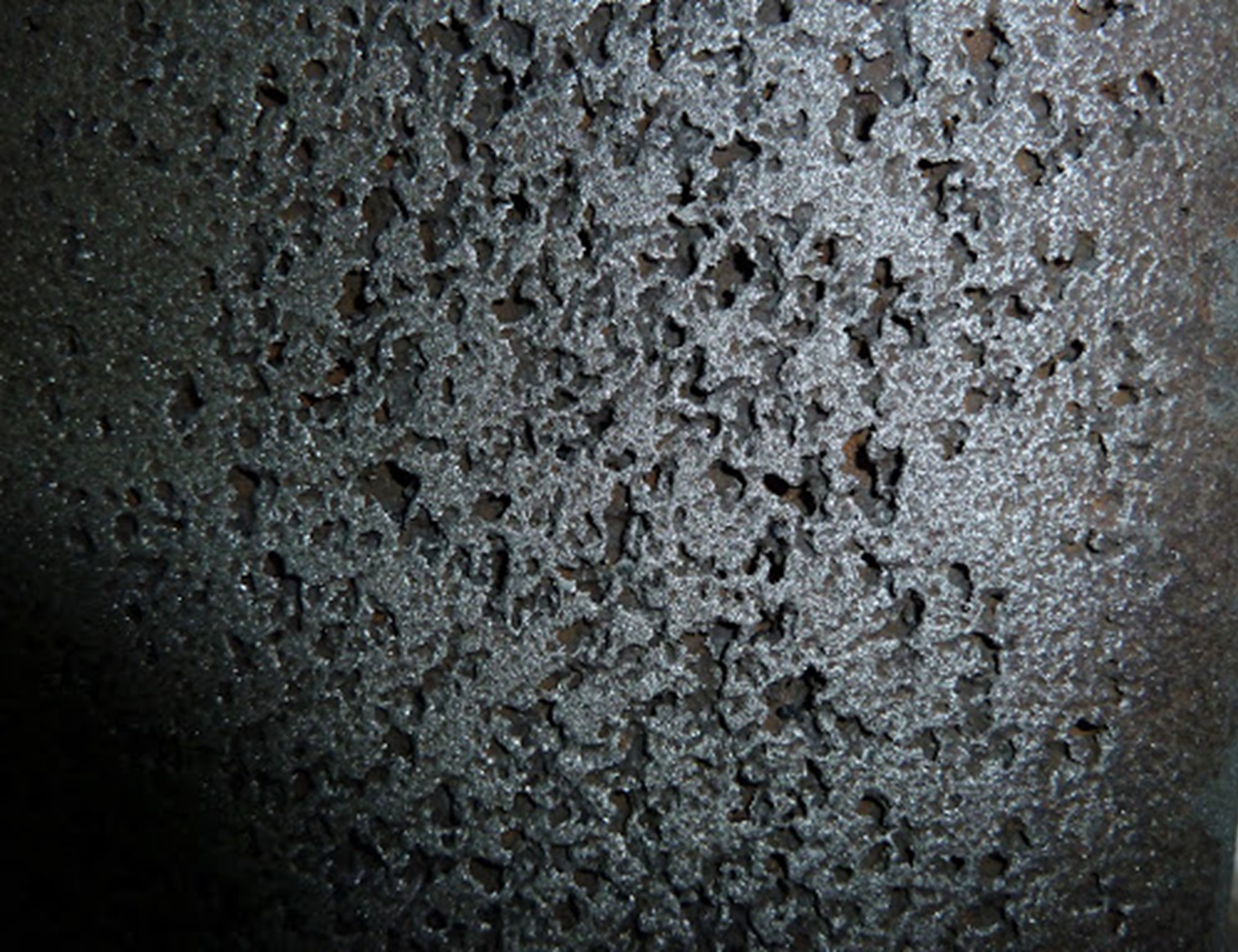
Possible pump damage cause by cavitation
Cavitation is a process, chain reaction of damaging effects one after the other which ultimately leads to pump destruction.
However, it is worth mentioning that possible damages to AODD pumps aren’t as devastating and expensive as in other types of pumps. Damage most likely will be limited only to diaphragms. Very rarely valves and pump body are damaged. However, cavitation in AODD pump will significantly increase operational cost.
The cost of pumping one liter of liquid will increase – when the pump is cavitating, less liquid is being pumped per pump stroke (liquid is mixed with vapor bubbles). However, the same amount of energy is used to run the pump as in normal condition.
Portion of useful lifetime of the diaphragms will be consumed unproductively due to reduced volume of liquid per stroke.
Less volume per stroke can cause disturbance in the proper operation of equipment or production lines. Pump won’t be able to deliver early selected, constant amount of fluid.
Severe cavitation is recognizable by a characteristic noise, as if gravel is passing through the pump – result of vapor bubble implosions within the pump. Excessive pipes tremble is another sign of possible severe pump cavitation.
Mild cavitation may cause reduction of pump efficiency and moderate wear of pump parts without damaging pump completely.
Note: In Diaphragm pumps capacity loss often attributed to the mild cavitation is in fact a result of fluid acceleration (acceleration head) into the suction on each suction stroke. A pulsation dampener located in the proximity at the suction of the pump will solve the acceleration head problem.
How to prevent pump cavitation?
Basically, there are no materials which can resist cavitation. Even the most durable material is not able to withstand cavitation for a long time. Plastics and aluminium will be destroyed very quickly. Cast iron copes poorly with cavitation due to the rapid destruction of graphite inclusions. Only Stainless Steel can resist cavitation for a while.
Fortunately, the effect of cavitation on the pump can be minimize or prevented by optimization pumping system design, or use equipment specially designed for applications with negative NPSHa (not an option for Air Operated Diaphragm pumps).
For AODD pumps optimization of the pumping system is the only way to combat cavitation. Pump cavitation occurs when the pressure in the pump inlet drops below the vapor pressure of the liquid. Vapor bubbles form at the inlet of the pump and are moved to the discharge of the pump where they collapse. To prevent / minimalize cavitation in AODD pump:
1. NPSHa > NPSHr
NPSHa (Net Positive Suction Head, available – NPSH provided by the piping system) must be greater than pump NPSHr (Net Positive Suction Head, required – the minimum pressure required at the suction port of the pump to keep the pump from cavitating). Cavitation is avoided (fluid starved suction condition is avoided) when NPSHa > NPSHr.
NPSHa value of the piping system must be calculated every time, whereas NPSHr is a function of the pump. NPSHr values for Air Operated Diaphragm pumps are different, depending on the manufacturer, pump size, type of diaphragm (values for PTFE diaphragms differ from the others).
Needless to say, that for defining NPSH value characteristic of the fluid must be taken into account – specific gravity, viscosity, temperature.
When calculating pump NPSH required one factor is frequently overlooked – fluid vapor pressure. Fluids with high vapor pressures ( liquids which tend to evaporate readily from an open container) often form vapor upstream of the pump. Many applications with these fluids operate at so large NPSH deficit from the start, that the system will never be able to compensate it. Examples of fluids with high vapor pressures:
• Acetaldehyde
• Acetone
• Allyl chloride
• Anhydrous Ammonia
• Benzene
• Bromine
• Carbon disulphide
• Chloroform
• Ethyl alcohol
• Gasoline
• Hexane
• Liquefied Petroleum Gas (LPG)
• Methyl acetate
• Methylene chloride
• Pentane
• Various types of refrigerants and condensates
2. Pumping set up conditions
Pumping installation must be properly designed. An NPSH deficit can be created by poorly designed pumping setup conditions. In such a case even low vapor pressure fluids like water, lube oil or diesel fuel can transit to vapor and create “boiling fluid”. There are several pumping setup conditions at which NPSH deficit – cavitation is highly probable:
• Excessive length of suction pipe
• Sucking from excessive depths
• Flow restrictions at the inlet – piping elbows, reducers, clogged filters and strainers, too large curvature of the pipeline, partially closed valves
• Undersized piping – pipes dimensions should be equal or greater than the diameter of the suction connection of the pump
3. Pump performance monitoring
We can prevent or minimize cavitation by analyzing where the working points of the pump are on the curve. If they don’t follow the curve line, pump may have problem with cavitation.
Next, finding the cavitation point by opening air valve and start pump slowly. Then by carefully increasing capacity reach the point in which further opening of the air valve increases cycling rate without increasing fluid discharge volume. This will be cavitation point of the pump, and at this point air valve should be slightly closed.
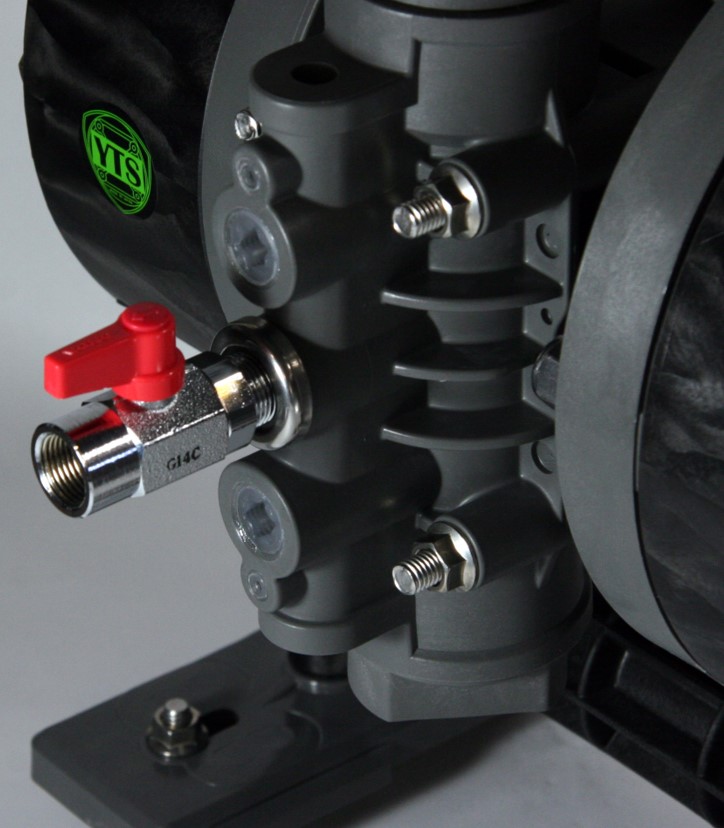
If there is a need of further increase of pump capacity, the following actions should be taken as individual or in combination:
• Increase diameter of the suction line
• Reduce suction line length
• Reduce suction depth
• Lower the temperature of the liquid
• Use larger size pump
• Use pumps in a series
We’ve got something exciting to tell you!
HELLO SWEDISH! We’re excited to announce that we’ve just launched Swedish language support on our website! This new addition to our language family has been
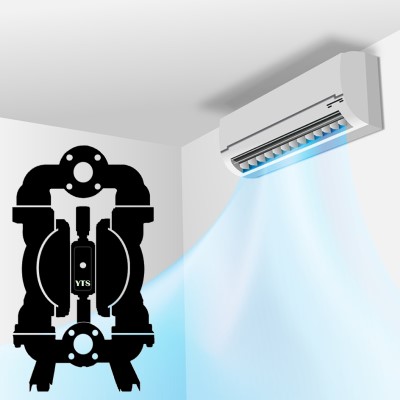
Indoor Air Quality
Indoor Air Quality (IAQ) – air quality within and around buildings and structures plays is of utmost importance not only for employees well-being and ability
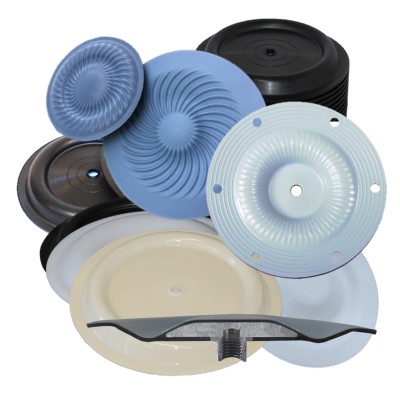
10 Factors to Consider When Selecting Diaphragm
Diaphragms are one of the most important elements of Air Operated Double Diaphragm Pump. They separate the wetted side (fluid side) of the pump from
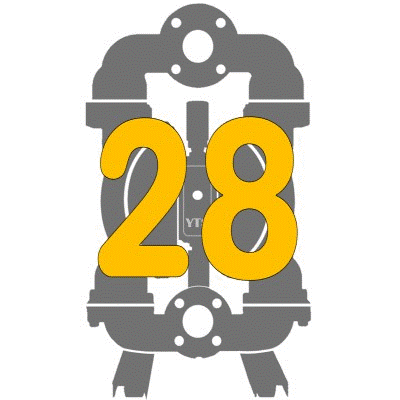
28 Reasons Why Use Air Diaphragm Pump
Air Diaphragm Pumps are so much versatile in design, materials, performances and functions, that they can handle most types of fluids. They are used for
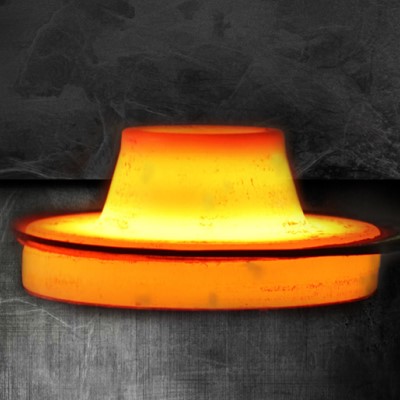
Hastelloy Air Diaphragm Pumps
The primary function of Hastelloy C-22 (also known as a “superalloy” or “high-performance alloy”) is a long-lasting survival in severely corrosive, or erosion prone environments,
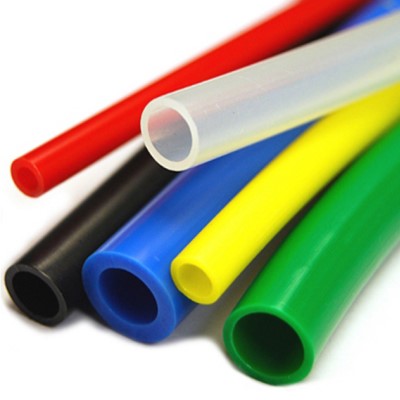
Too Small Size of Air Supply Line to the Air Diaphragm Pump
It is not uncommon to use too small air supply line when installing an Air Operated Diaphragm pump. Overlooking restrictions installed along the line, which