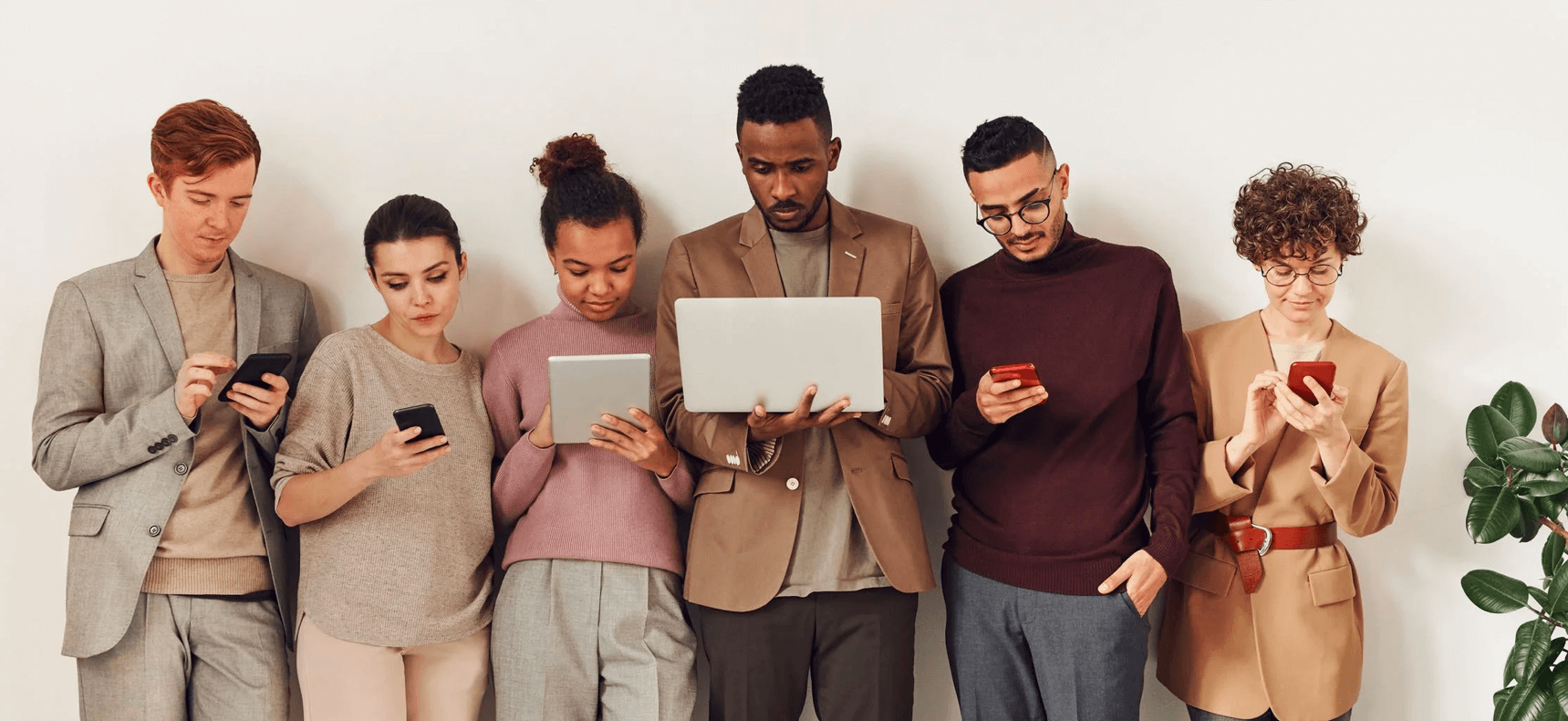
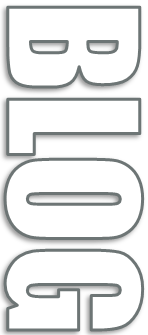
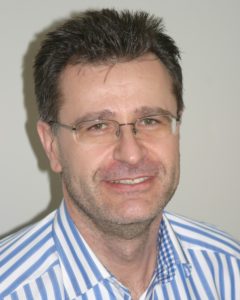
Written by Rick
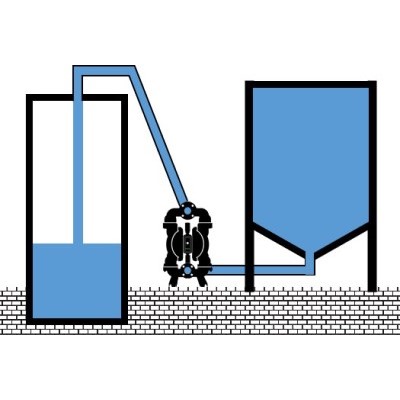
Too High Positive Inlet Pressure to the Pump
This is the first article from the cycle – 12 ways how to kill your Diaphragm Pump. Contrary to the article title this is something, that nobody wants to do. In our articles we want to point out problems which may damage your pump, installation or significantly reduce lifetime of wearing parts. Diaphragm Pumps are widely used in transfer applications. To pump fluid from tanks storage location to the production area.
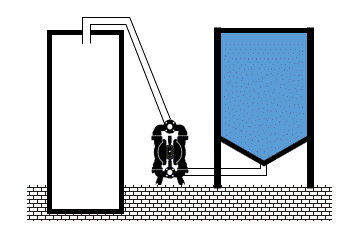
Attention should be paid to this type of installation due to limits on the amount of positive inlet pressure to the pump. Particular attention is required in those cases in which PTFE diaphragms are used. Typically, PTFE diaphragms can handle maximum 0,6 bar of positive inlet pressure (Net Positive Suction Head – NPSH).
When the AODD pump is located at the bottom of the storage tank is very easy to reach and overcome the limit of permissible positive inlet pressure. NPSH should be carefully calculated taking into account the height of the storage tank and the specific gravity of the fluid. Those two combined factors produce a static inlet pressure.
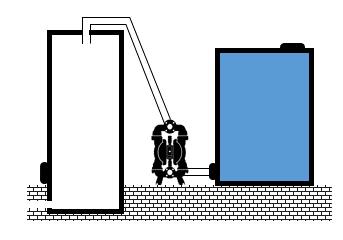
Often this fact is neglected when building an installation and choosing a pump. Specific gravity of many fluids significantly exceeds specific gravity of water (all information about pumps performance or limitations given by pumps manufacturers are always based on water – specific gravity 1g/cm3). For example: Sulfuric Acid 98% – 1,835 g/cm3, Nitric Acid 70% – 1,42 g/cm3, Phosphoric Acid 90% – 1,75 g/cm3, etc. At the 80% of maximum positive inlet pressure diaphragm lifetime will start to shorten significantly.
The real problem starts when pump is running. Each time the ball valve is closed, the fluid velocity created from the inlet stroke is abruptly stopped. This creates a water hammer effect which produces high pressure spikes, and Diaphragm Pump can create pressure spikes up to four times the static NPSH pressure. With such a force in action PTFE diaphragms lasts day, maximum weeks. Diaphragm failure can cause pump damage when fluid enters dry part of them pump. And due to the fact that many fluids are highly aggressive such a failure can also cause significant damage to the facility and be harmful for people.
Overall financial costs as a result of diaphragm failure could be very high. Fluid inlet positive pressure can be very destructive. When is close to the diaphragm permissible limit, shortens its lifetime radically. When exceeds limits, pump and installation can be damage and people at risk.
We’ve got something exciting to tell you!
HELLO SWEDISH! We’re excited to announce that we’ve just launched Swedish language support on our website! This new addition to our language family has been
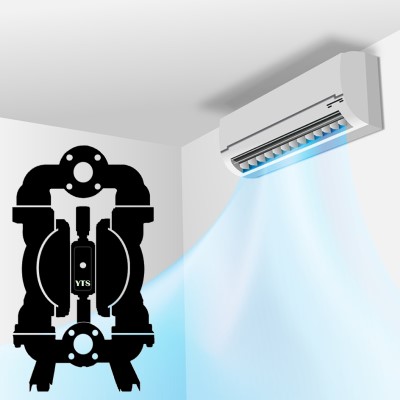
Indoor Air Quality
Indoor Air Quality (IAQ) – air quality within and around buildings and structures plays is of utmost importance not only for employees well-being and ability
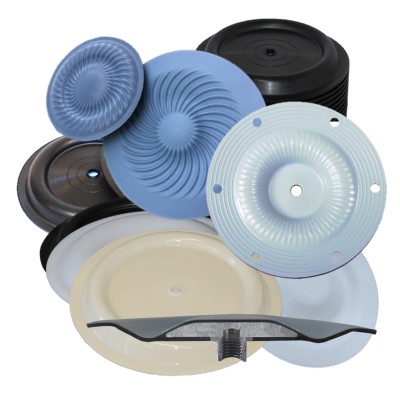
10 Factors to Consider When Selecting Diaphragm
Diaphragms are one of the most important elements of Air Operated Double Diaphragm Pump. They separate the wetted side (fluid side) of the pump from
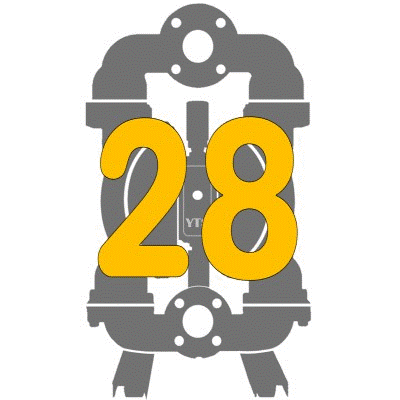
28 Reasons Why Use Air Diaphragm Pump
Air Diaphragm Pumps are so much versatile in design, materials, performances and functions, that they can handle most types of fluids. They are used for
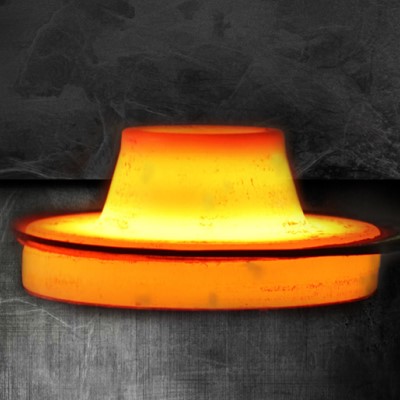
Hastelloy Air Diaphragm Pumps
The primary function of Hastelloy C-22 (also known as a “superalloy” or “high-performance alloy”) is a long-lasting survival in severely corrosive, or erosion prone environments,
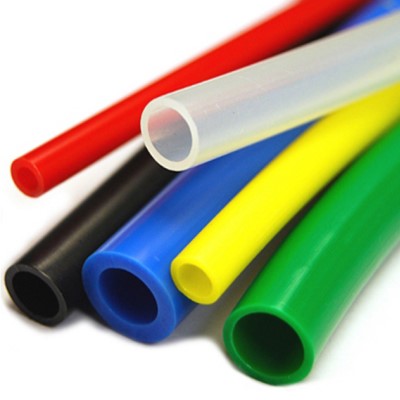
Too Small Size of Air Supply Line to the Air Diaphragm Pump
It is not uncommon to use too small air supply line when installing an Air Operated Diaphragm pump. Overlooking restrictions installed along the line, which