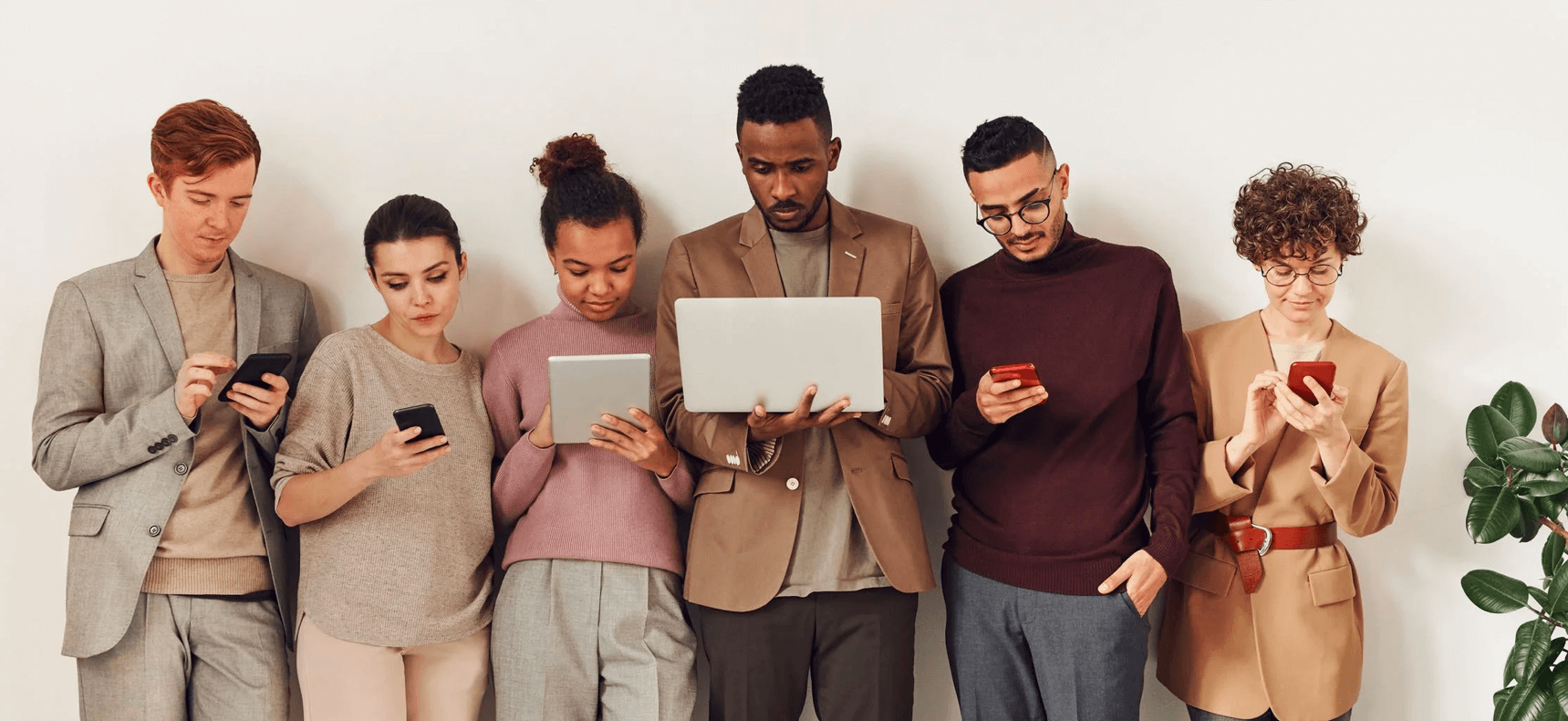
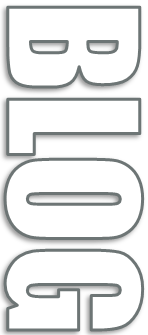
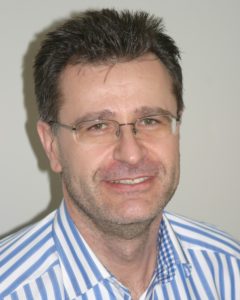
Written by Rick
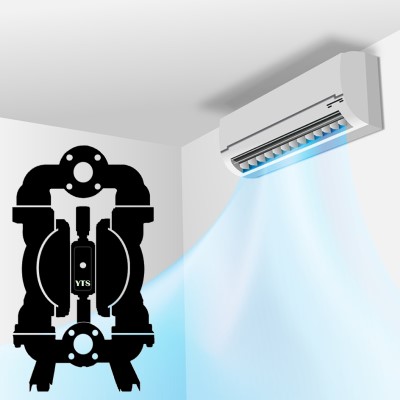
Indoor Air Quality
Indoor Air Quality (IAQ) – air quality within and around buildings and structures plays is of utmost importance not only for employees well-being and ability to work but also for the proper operation of Air Operated Diaphragm Pumps (like other pneumatic and electronic equipment). Temperature, humidity, amount of outside air, mold on air, airborne contaminants all play a role in IAQ.
There are ongoing researches that increasingly links airborne hazards and pollution dangerous to manufacturing workers to the worsening of Covid-19 symptoms.
The most sensitive part of all Diaphragm Pumps is an Air Motor. Air Motor with Air Valve at the center of the pump directs compressed air alternately to two air chambers located on the opposite sides of the pump. Bad quality of the air – chemically, biologically, dust/dirt, humidity – will damage Air Motor elements and cause downtime of the pump and the need for its repair.
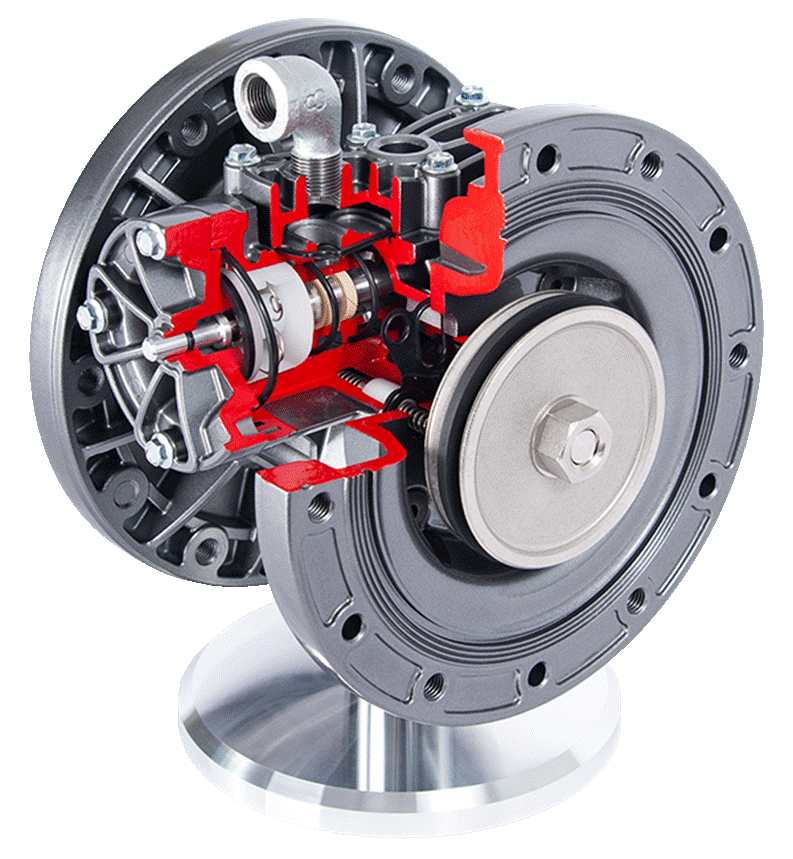
Chemical Contamination of the Air
Chemical fog, smoke, mists, gases, vapors, sprays strongly affect employees, but also some components of Air Motor. All sealing materials (gaskets, o-rings) used in Air Motor are particularly exposed to negative effects of vapors of incompatible chemicals.
Especially users of AODD pumps in the chemical industry should be aware of the potential risk to the Air Motor from chemically contaminated air. Manufacturers of:
• Base chemicals
Petrochemicals and derivatives, basic inorganics and polymers. In petrochemical installations various fractions of distillation products may be encountered in the air – carcinogens 1,3-butadiene, benzene, residues of toluene and xylenes. In badly vented, confined spaces they constitute the risk to staff and equipment.
• Specialty chemicals
Active ingredients and co-formulants for the pharmaceuticals industry and plant protection, auxiliaries for industrial processes, paints and inks, biocides, and dye and pigments. In the production of plastics and resins, the manufacture of paints and adhesives involves the presence of residues of highly toxic intermediate products, such as mono-isocyanates (polyurethanes), vinyl chloride (PVC), epichlorohydrin (epoxy resins), ethylene oxide.
• Consumer chemicals
Soaps and detergents, perfumes and cosmetics. Glycol ethyl ether (Cellosolve) isn’t chemically compatible with many rubber materials of sealing – NBR, EPDM, FKM, CR.
Also, toxic gases, vapor or fumes may be generated by certain maintenance or repair activities. For example, the formation of toxic phosgene (Carbonyl Chloride) as a result of welding activities, when residues of chlorinated solvents are present as a result of cleaning and degreasing. Phosgene fumes severely damage EPDM and Neoprene sealings.
When there is a high chemical concentration in the air also the pump body shell (Aluminium, Cast Iron, Polypropylene) may be a subject of gradual vapor corrosion. However, this negative effect of toxic vapor on aluminium dry, mid section of the pump can be prevented by using protective coating.
YTS offers special protective PTFE and Nickel coating of all aluminium elements of the dry section of the diaphragm pump.
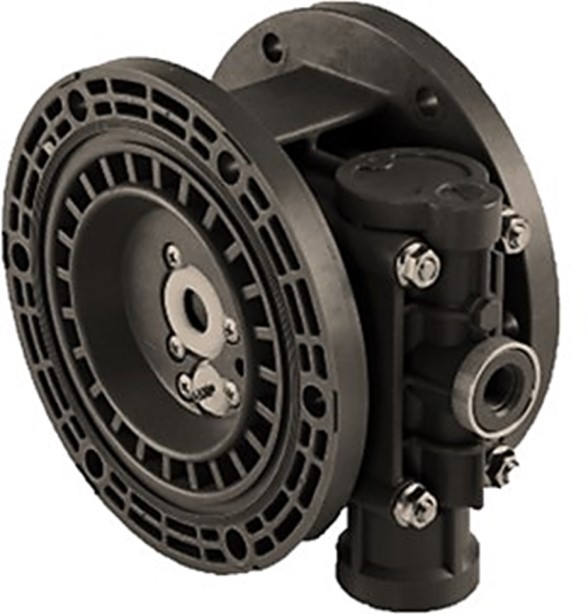
Biological Contamination of the Air
Microbial pollution of indoor air comes from hundreds of species of bacteria, fungi and molds that grow indoors when sufficient moisture is available. AODD pumps works in different climatic environments using local air, which might be contaminated. Pumps working in confined spaces among people may spread biological contaminants, they are using a lot of air which leaves the pump after the work is done.
It is important to monitor the air quality and not to make the pump fed with biologically polluted compressed air, which will lead to the immediate spread of contaminants throughout the production area.
Particularly now, during Covid-19 pandemic, it is important to pay attention to the biological quality of the air supplied to the pumps.
Dust/Dirt the Air
This is the most common cause of damage to an air motor and pump.
Many technological processes create airborne dust hazards – batching, mixing, blending, coating, crushing, drying, salting, milling, conveying are just a few of many. Accumulation of dust/dirt inside the air motor will lead to the clogging of the air valve or muffler.
Unseen dust remains suspended in the air for a long period of time. When air with dust is used by the compressor it may damage AODD pump, and via pump may be introduced to employees.
Industrial processes that generate industrial dust include ceramics production, paint and ink production, metallurgical work, 3D printing, welding, fertilizers production, plasma and laser cutting, abrasive blasting, glass production, chemical processing, food processing, pharmaceutical, woodworking, extrusion of plastics and metals. Also, weighing, bagging, and transporting powdered materials.
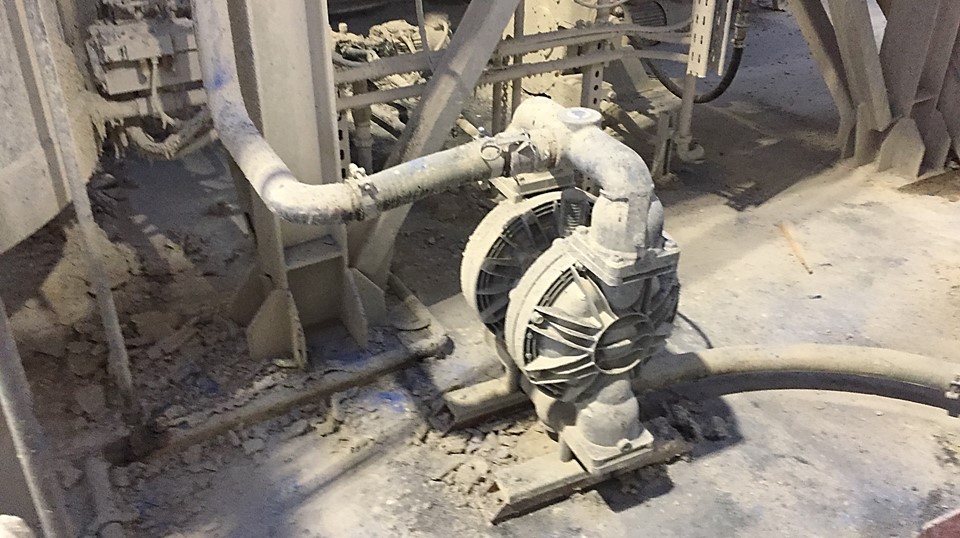
Process dust is generated during manufacturing operations such as cutting, drilling, grinding, sawing, welding, and plasma cutting.
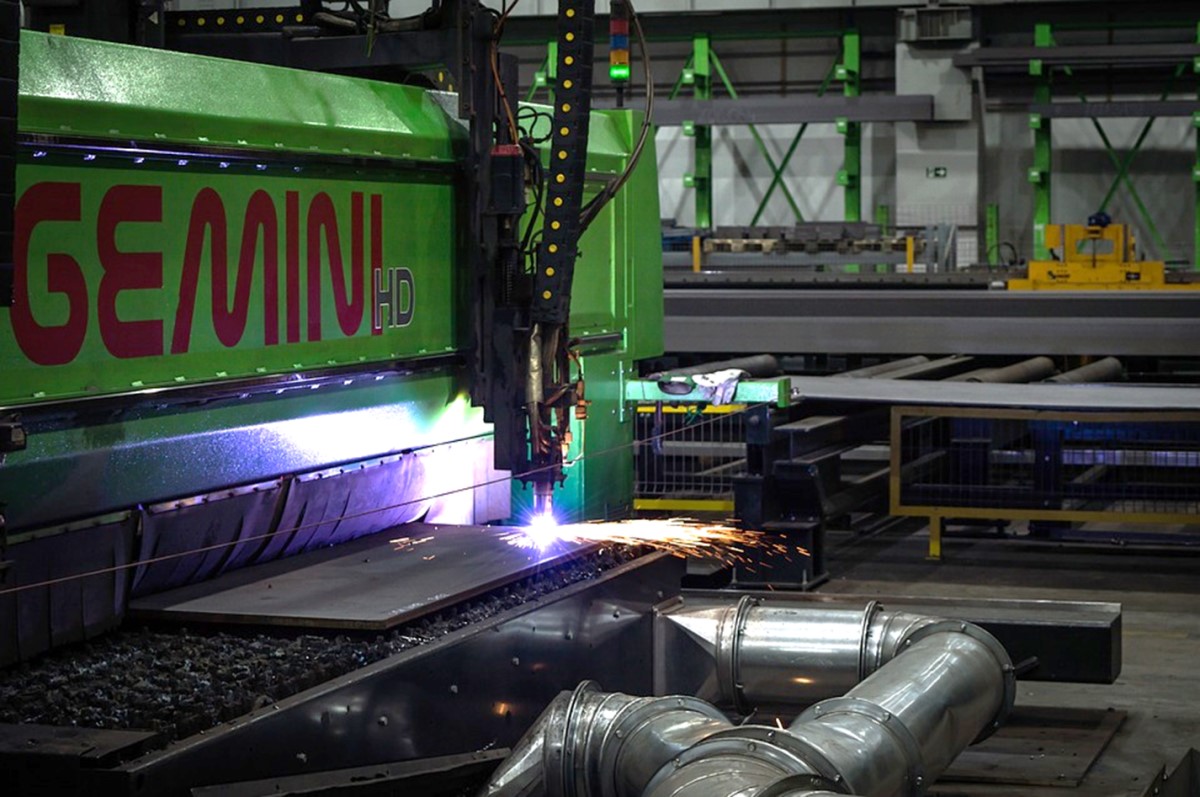
Humidity of the Air
Dust or dirt combined with a small amount of moisture can form glue like substance inside air motor blocking air supply channels. Especially prone to this are all AODD pumps, in which grease prepacked in the factory is used inside air motor. Dust and dirt are retained by the grease forming a thick substance.
To prevent this clean, dry, filtered air should be used. Filter regulator should be installed on the air supply line.
Summarizing
Poor indoor air quality will impact AODD pumps, but more importantly the health of employees. It can result in increased absenteeism, reduced productivity and potential safety hazards.
AODD pumps due to principle of operation – compressed air is used to power the pump – may accelerate the spread of contaminants in the pump work area. Especially in badly vented, confined production areas.
We’ve got something exciting to tell you!
HELLO SWEDISH! We’re excited to announce that we’ve just launched Swedish language support on our website! This new addition to our language family has been
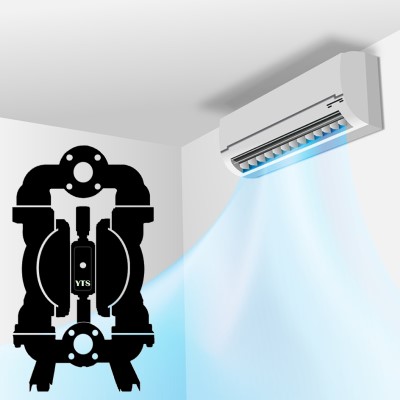
Indoor Air Quality
Indoor Air Quality (IAQ) – air quality within and around buildings and structures plays is of utmost importance not only for employees well-being and ability
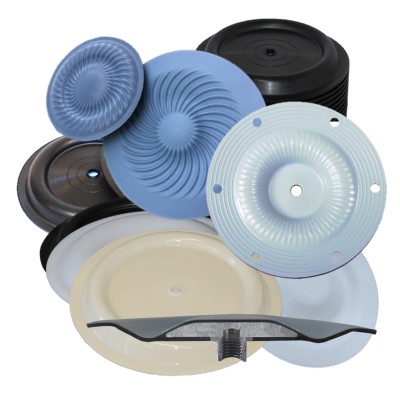
10 Factors to Consider When Selecting Diaphragm
Diaphragms are one of the most important elements of Air Operated Double Diaphragm Pump. They separate the wetted side (fluid side) of the pump from
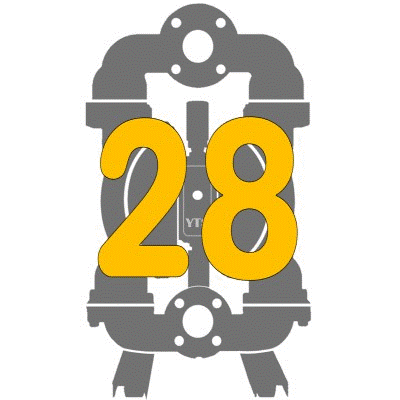
28 Reasons Why Use Air Diaphragm Pump
Air Diaphragm Pumps are so much versatile in design, materials, performances and functions, that they can handle most types of fluids. They are used for
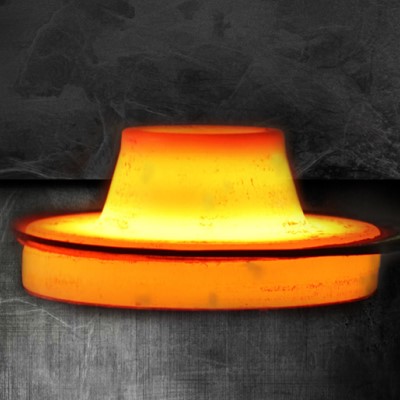
Hastelloy Air Diaphragm Pumps
The primary function of Hastelloy C-22 (also known as a “superalloy” or “high-performance alloy”) is a long-lasting survival in severely corrosive, or erosion prone environments,
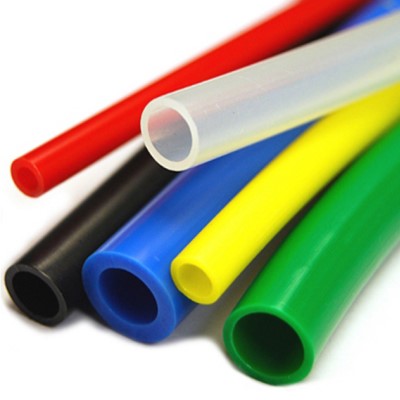
Too Small Size of Air Supply Line to the Air Diaphragm Pump
It is not uncommon to use too small air supply line when installing an Air Operated Diaphragm pump. Overlooking restrictions installed along the line, which