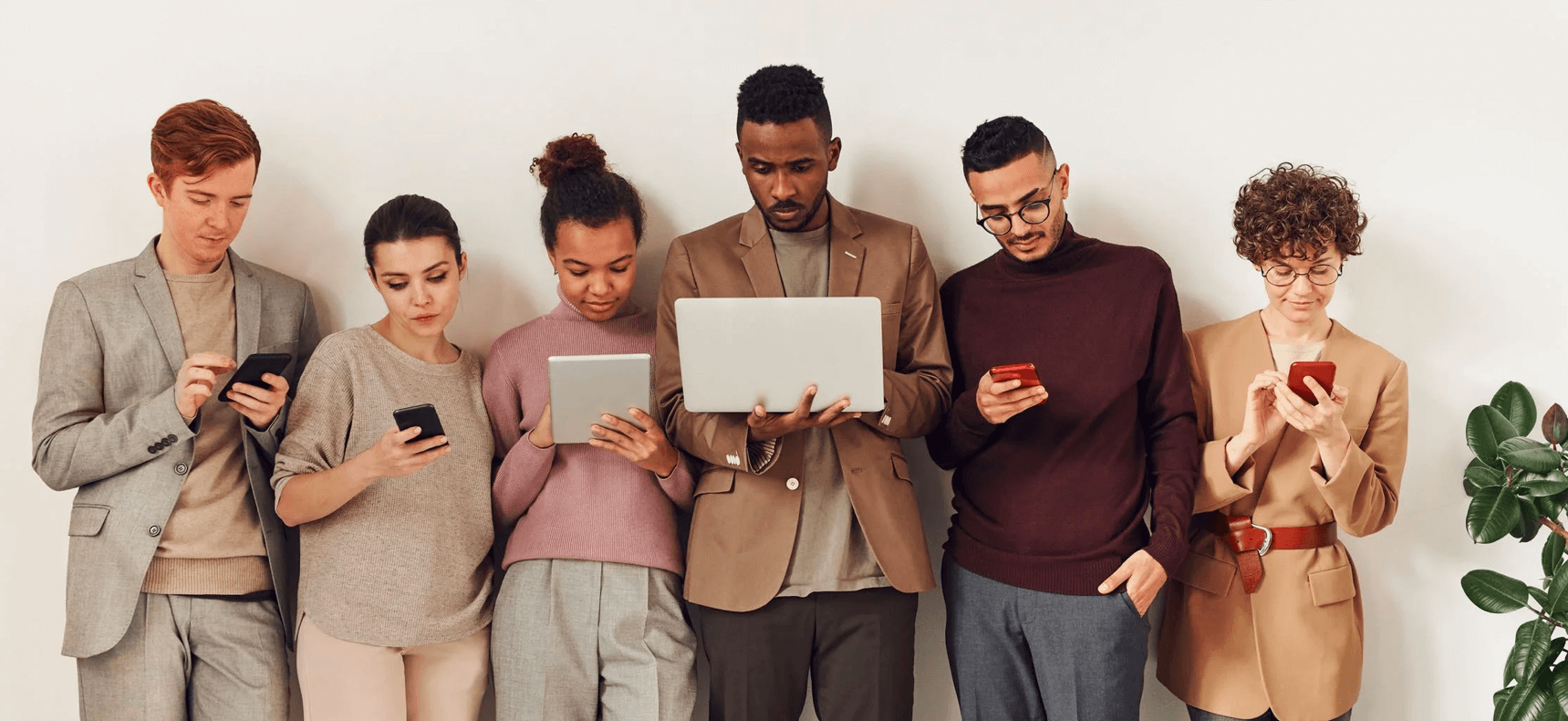
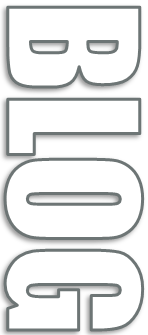
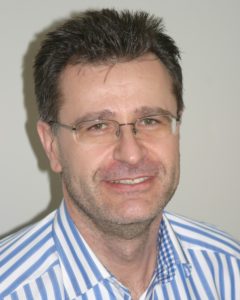
Written by Rick
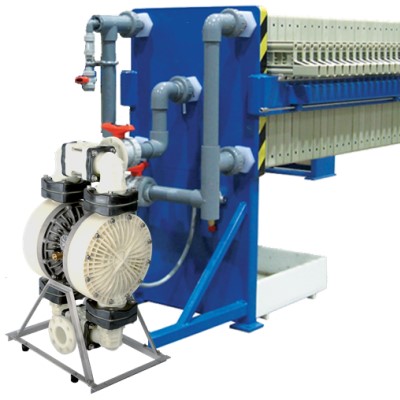
Feed Pumps for Filter Press
Air Operated Double Diaphragm Pumps are commonly used as a feeding pumps in filter press applications due to:
- Their versatility. Diaphragm pumps can handle different chemicals, viscous fluids, abrasive, corrosive and solid and sludge-like fluids.
- They do not require electricity.
- Diaphragm pumps are designed to provide a constant, non-stalling operation. As the pressure builds in the chamber pump is self-regulating and will stop at a predetermined pressure. As the pressure is released in the tank the pump will self-prime and return to its original flow rate.
- Pump can run dry without fluid. This won’t damage the pump. This feature is very important, because filter press systems often become blocked due to the viscosities of the liquid being pumped, causing the pump to run dry.
- AODD pumps can work against closed discharge valve (dead head application).
- Diaphragm pumps don’t have any drives, rotating parts nor rotary shaft seals.
- Diaphragm pump start-up is very simple, because pumps are completely self-priming (dry-start on suction lifts).
- They are easy to install, maintain and not expensive.
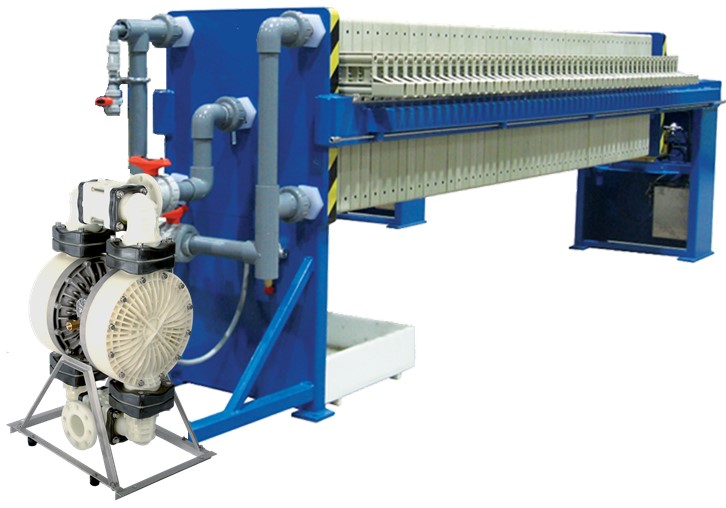
The effectiveness of the filtration process largely depends on a properly selected pump. Pump parameters affect the speed of filling the filter and the wear of the filter cloth. The humidity of the cake depends on the pressure that the pump creates.
Filter press is prepared for operation by tightly clamping the filter plates together using the hydraulic pump. Once the press is closed the AODD feed pump is turned on, forcing the slurry or sludge into the filter chamber. Under pressure the particles are uniformly deposited on the filter cloths. The initial deposited layer of solids becomes the filtering media. As operation continues the deposited solids layer continues to build forming the filter cake.
The filtrate passes through the filter cloths and is channeled to the discharge ports. As the filter press cycle continues the filtrate clarity will gradually improve until a clear effluent is produced. As the filter cake continues to build the AODD pump will continue to slow. A predetermined pump rate decrease indicates that the press is full (AODD pump will get to 30 second to one minute intervals between thrusts, indicating that pressure has increased due to solids building up inside the press cavities).
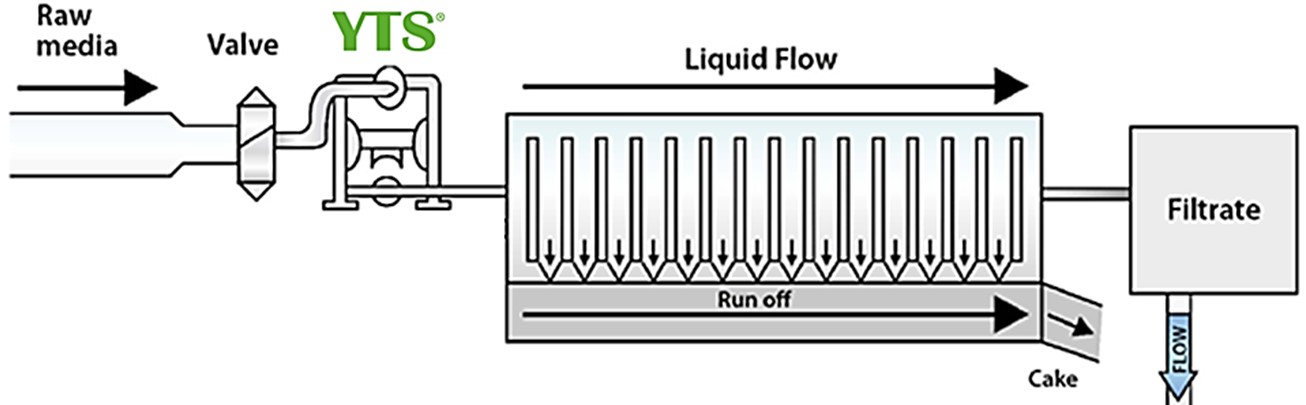
YTS pumps have the same common features of AODD pumps, but additionally they poses several unique attributes. These unique features makes YTS pump perfect feed pump for filter press. One of these unique features is Reset Button.
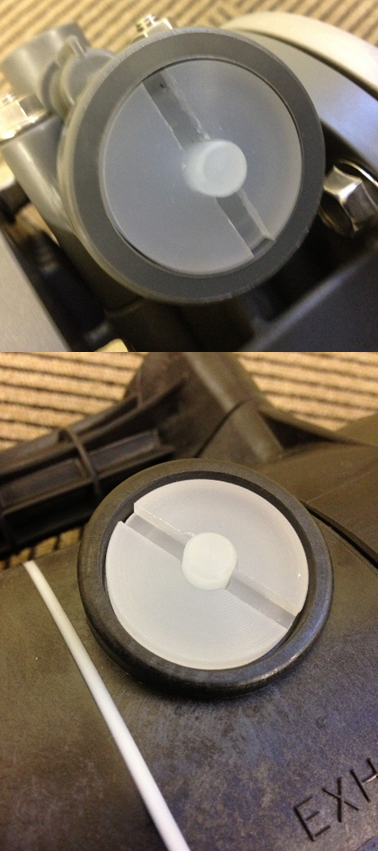
When pump will get to 30 second to one minute intervals between thrusts (what indicates that pressure has increased due to solids building up inside the press cavities). And finally will stop (due to pressures equalization – dead heading). Then, by pressing Reset Button YTS pump can make few additional strokes overcoming back pressure inside the filter press.
By this, the filter press filtration efficiency could be improved by 5-10% (depending on the pump size and filter press).
YTS Diaphragm pumps are truly non lubricated and not factory prepacked with grease. In YTS pumps:
- There is no dirt sticking on Air Spool Valve, sleeve and pilot valves
- No glue formation (moist + oil) in Air Spool Valve
- No blocked air channels caused by dirt sticking
- No contamination of pumped fluids in case a diaphragm ruptures
- No cost of lubrication oil
- No labor cost to fill the oil bottles
- No pollution of the environment
- No oil spray causing slippery surfaces
- Less cleaning of the production area
Short Stroke Design is an another feature of YTS pumps, important for filter press systems.
Short stroke design eliminates a lot of diaphragm internal stress because YTS pumps doesn’t have to overcome the mechanical stiffness of the diaphragms.
Bigger diaphragm surface in YTS pumps helps to start up a pump at a lower air pressure.
Long stroke design is commonly used worldwide as the standard for AODD design. Many of our competitors have to overstretch their diaphragms. This creates a lot of internal stress, because mechanical stiffness of diaphragms must be overcome. The smaller diaphragm surface is creating so much resistance, that those pumps need a much higher air pressure to start up.
We have wide array of Air Operated Double Diaphragm Pumps that can be used as a feed pump in filter press systems. 2:1 High Pressure pumps, that can produce almost 17 bar air pressure, Metallic Pumps with maxumum air pressure 8,5 bar and 7 bar, Plastic Pumps with maximum air pressure of 7 bar.
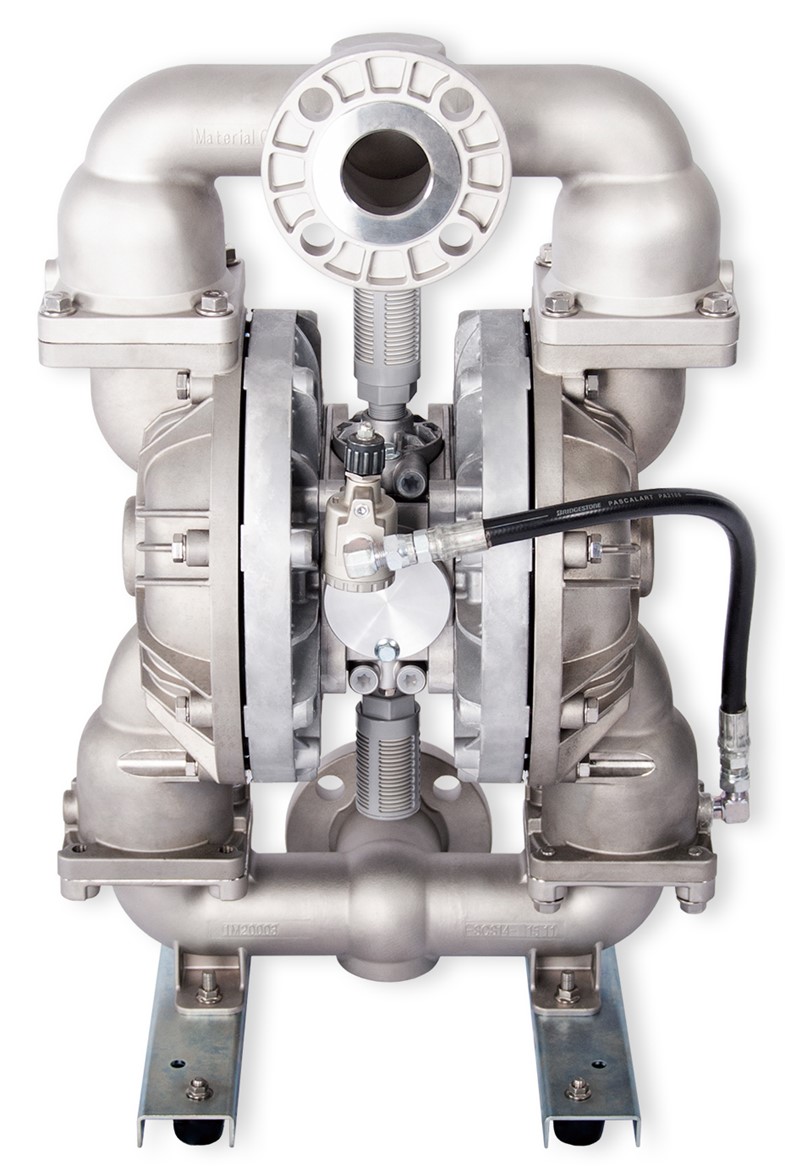
We’ve got something exciting to tell you!
HELLO SWEDISH! We’re excited to announce that we’ve just launched Swedish language support on our website! This new addition to our language family has been
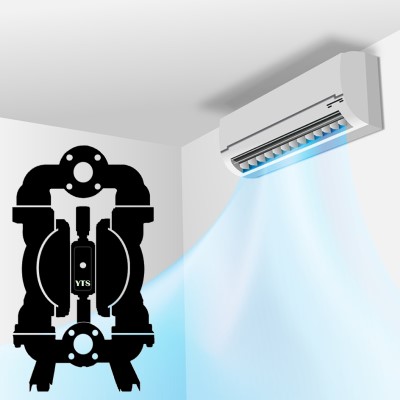
Indoor Air Quality
Indoor Air Quality (IAQ) – air quality within and around buildings and structures plays is of utmost importance not only for employees well-being and ability
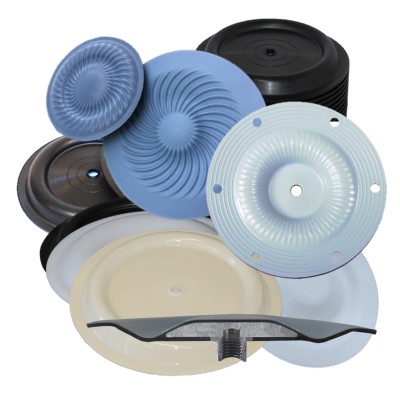
10 Factors to Consider When Selecting Diaphragm
Diaphragms are one of the most important elements of Air Operated Double Diaphragm Pump. They separate the wetted side (fluid side) of the pump from
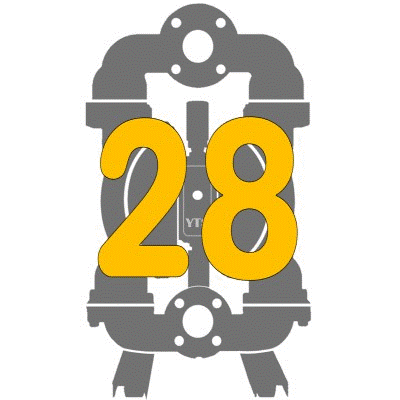
28 Reasons Why Use Air Diaphragm Pump
Air Diaphragm Pumps are so much versatile in design, materials, performances and functions, that they can handle most types of fluids. They are used for
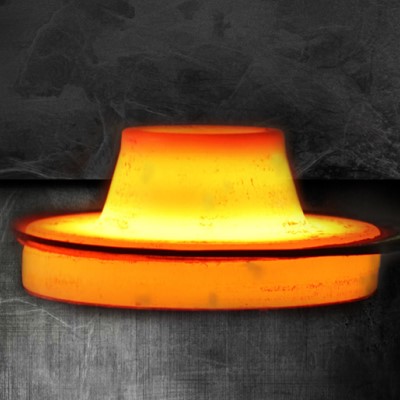
Hastelloy Air Diaphragm Pumps
The primary function of Hastelloy C-22 (also known as a “superalloy” or “high-performance alloy”) is a long-lasting survival in severely corrosive, or erosion prone environments,
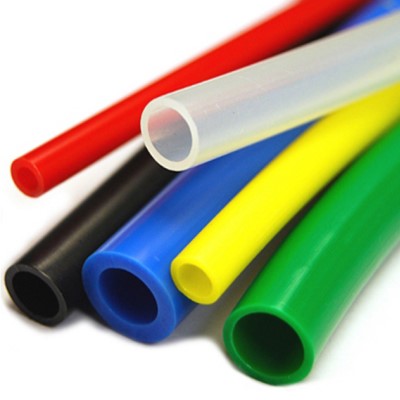
Too Small Size of Air Supply Line to the Air Diaphragm Pump
It is not uncommon to use too small air supply line when installing an Air Operated Diaphragm pump. Overlooking restrictions installed along the line, which
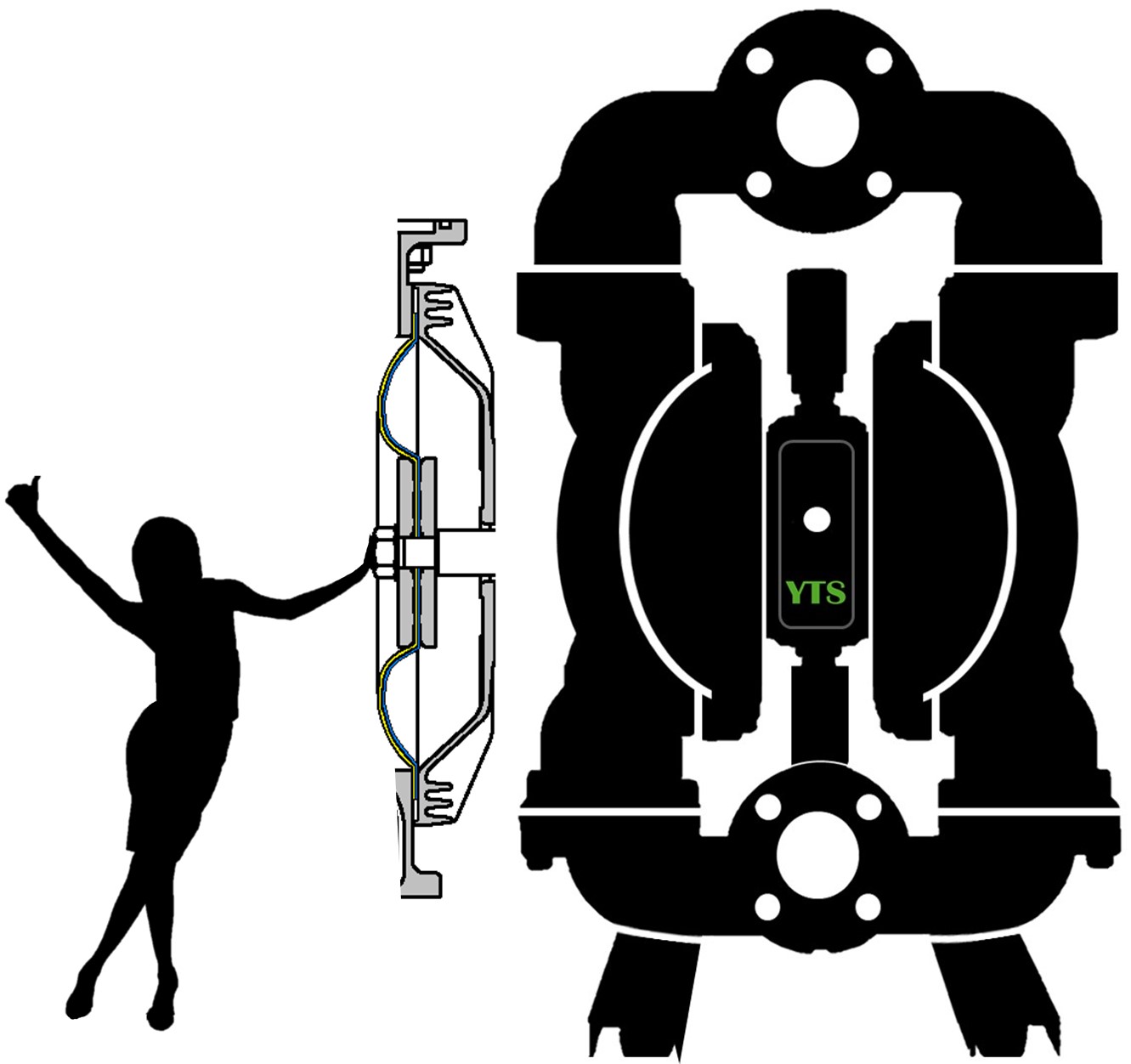